Covalent layer-by-layer self-assembling process for constructing polymer film on planar substrate
A layer-by-layer self-assembly, polymer film technology, applied in chemical instruments and methods, lamination, layered products, etc., to achieve the effects of fast reaction speed, high temperature stability, and stable structure
- Summary
- Abstract
- Description
- Claims
- Application Information
AI Technical Summary
Problems solved by technology
Method used
Image
Examples
Embodiment 1
[0031] Soak the silicon chip in 40% hydrofluoric acid for 10 seconds, rinse it with water, dry it and suspend it above the dry toluene solution of 1% aminopropyltriethoxysilane, heat the solution to boil for 1 hour, Take it out to get an aminated silicon wafer. Put the aminated silicon wafer in a tetrahydrofuran solution of 4 mg / ml polyglycidyl methacrylate, and use an oil pump to evacuate until no bubbles are generated on the substrate. Then seal it, shake it at 20°C for 10 hours, then take it out, and wash it several times in ultrasonic with tetrahydrofuran. Put the silicon wafer into the aqueous solution of 4mg / ml polyallylamine, pump the vacuum with the water pump until no air bubbles are generated on the silicon wafer, then seal it, shake it at 20°C for 10 hours, then take it out, and immerse it in the ultrasonic wave with water. Wash several times. Repeat the above process to obtain polymer films assembled with 4 layers, 8 layers, 12 layers and 16 layers. The ellipsom...
Embodiment 2
[0033] Soak the silicon chip in 10% hydrofluoric acid for 10 seconds, rinse it with water, dry it, suspend it above the dry toluene solution of 5% aminopropyltrimethoxysilane, heat it until the solution boils for 2 hours, take it out, Aminated silicon wafers were obtained. Put the aminated silicon wafer in a 1mg / ml tetrahydrofuran solution of polyglycidyl methacrylate, evacuate it with a water pump until no bubbles are generated on the silicon wafer, then seal it and shake it at 60°C for 0.5 hours , then removed and cleaned several times in ultrasonication with acetone. Put the silicon wafer into the aqueous solution of 1 mg / ml polyallylamine, pump the vacuum with water pump until no air bubbles are generated on the silicon wafer, then seal it, shake it at 60°C for 0.5 hours, then take it out, and use water to ultrasonically Wash several times. The above process was repeated 4 times to obtain an 8-layer polymer multilayer film. figure 2 (a) is the result of small-angle X-r...
Embodiment 3
[0035] Soak the silicon chip in 20% hydrofluoric acid for 2 minutes, rinse with water, dry it, suspend it above the dry toluene solution of 10% aminopropyltrimethoxysilane, heat it until the solution boils for 5 hours, take it out, and get Aminated silicon wafers. Put the aminated silicon wafer in 8 mg / ml tetrahydrofuran solution of polyglycidyl methacrylate, vacuumize it with a water pump until no bubbles are generated on the silicon wafer, then seal it, and shake it at 60°C for 0.5 hours , and then removed and cleaned several times in ultrasonic with chloroform. Put the silicon wafer into the aqueous solution of 8 mg / ml polyallylamine, vacuumize it with an oil pump until no air bubbles are generated on the silicon wafer, then seal it, shake it at 80°C for 0.5 hours, then take it out, and use water to ultrasonically Wash several times. The above process was repeated 6 times to obtain a 12-layer polymer multilayer film. figure 2 (b) is the result of the small-angle X-ray d...
PUM
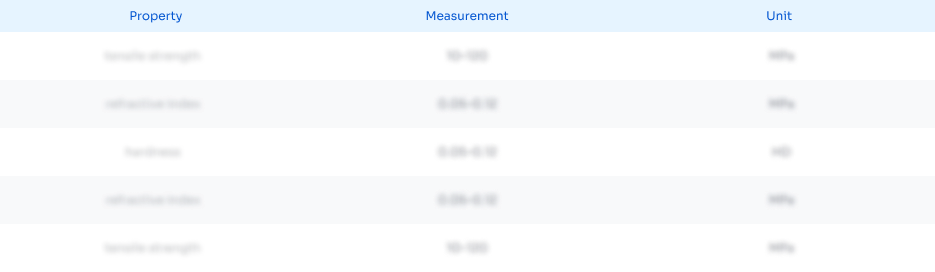
Abstract
Description
Claims
Application Information

- R&D Engineer
- R&D Manager
- IP Professional
- Industry Leading Data Capabilities
- Powerful AI technology
- Patent DNA Extraction
Browse by: Latest US Patents, China's latest patents, Technical Efficacy Thesaurus, Application Domain, Technology Topic, Popular Technical Reports.
© 2024 PatSnap. All rights reserved.Legal|Privacy policy|Modern Slavery Act Transparency Statement|Sitemap|About US| Contact US: help@patsnap.com