Method of producing cotton fiber product having smooth surfaces and cotton-regenerated cellulose compound yarn or fabric
A technology of regenerated cellulose and manufacturing method, which is applied in textiles and papermaking, plant fiber, fiber treatment, etc. It can solve the problems of not deep color, difficult dark color, white and fuzzy, etc., and achieve smooth fiber surface and excellent wrinkle resistance , the effect of quality improvement
- Summary
- Abstract
- Description
- Claims
- Application Information
AI Technical Summary
Problems solved by technology
Method used
Image
Examples
Embodiment 1-1
[0080]As a cloth made of cotton fibers, use a 0.1% by weight aqueous solution of an anionic-nonionic mixed active agent (manufactured by Nikka Chemical, Sunmol BH-75) at 80° C. for 20 minutes, and then use hydrogen peroxide (35%) 15% by weight and 0.2% by weight of sodium silicate and 0.1% by weight of sodium hydroxide aqueous solution bleached cotton fibers (30 single yarn) under the condition of 90 ℃ * 60 minutes plain weave fabric. The plain weave fabric was dipped in a 20°C aqueous solution containing 45% by weight of potassium hydroxide for 60 seconds without applying tension, and then subjected to two 10-minute hot water washes at 80°C. Next, neutralization was carried out at 80° C. for 10 minutes with a 0.05% by weight aqueous solution of acetic acid to completely remove the alkali. After that, SUMIFIX BLACK E-XF (manufactured by Sumitomo Chemical Industries, Ltd.) at a concentration of 5% owf (% by weight of the dye compound relative to the weight of the fiber) was use...
Embodiment 1-2
[0085] The same fabric as in Example 1-1 was immersed in 5% by weight of sodium hydroxide, 40% by weight of potassium hydroxide and an anionic surfactant (manufactured by Daido Synthetic Chemical Industry Co., Ltd. S0600) in a 5% by weight aqueous solution for 60 seconds, then perform two 10-minute hot water washes at 80°C, and then neutralize with 0.05% by weight acetic acid aqueous solution at 80°C for 10 minutes to completely remove the alkali. Then dye with the same prescription as Example 1-1. The evaluation results are shown in Table 1.
[0086] As shown in Table 1, by adding a surfactant as a penetrating agent, the surface tension of the treatment liquid becomes 30 dyn / cm 2 , and the same as Example 1-1 before adding surfactant, about 70dyn / cm 2 . In addition, the treatment was carried out until the coefficient of static friction was about 56% of the unprocessed product. In Example 1-2, all aspects of dyeability, gloss, and pilling were superior to those of Example ...
Embodiment 1-3
[0089] Tension was applied and treated under substantially the same conditions as in Example 1-2. That is, the same fabric used in Example 1-1 was immersed in 5% by weight of sodium hydroxide, 40% by weight of potassium hydroxide, and an anionic surfactant (manufactured by Daido Synthetic Chemical Industry Co., Ltd., Daido) under tension. 1 ルS0600) 5% by weight aqueous solution for 60 seconds, followed by two 10-minute hot water washes at 80°C, and then neutralized with 0.05% by weight acetic acid aqueous solution at 80°C for 10 minutes to completely remove the alkali. Then dye with the same prescription as Example 1-1. The evaluation results are shown in Table 1.
[0090] As shown in Table 1, although the treatment liquid was the same, by applying tension, the decrease in the coefficient of static friction was slightly larger than in the case of Examples 1-2. However, the dyeability, luster, pilling property, and touch were all the same as in Examples 1-1 to 2 and the like....
PUM
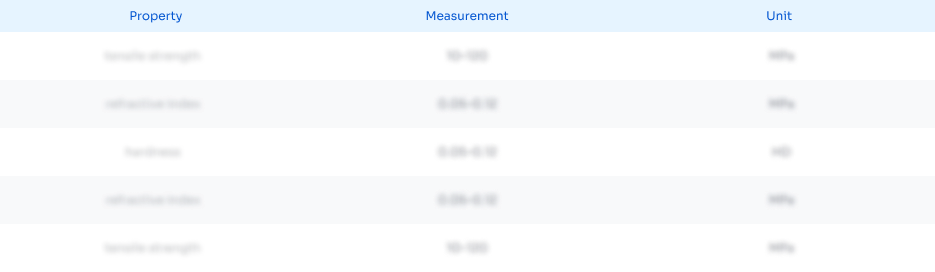
Abstract
Description
Claims
Application Information

- Generate Ideas
- Intellectual Property
- Life Sciences
- Materials
- Tech Scout
- Unparalleled Data Quality
- Higher Quality Content
- 60% Fewer Hallucinations
Browse by: Latest US Patents, China's latest patents, Technical Efficacy Thesaurus, Application Domain, Technology Topic, Popular Technical Reports.
© 2025 PatSnap. All rights reserved.Legal|Privacy policy|Modern Slavery Act Transparency Statement|Sitemap|About US| Contact US: help@patsnap.com