Catalyst for preparing cyclohexene by benzene hydrogenation, its preparing method and using method
A catalyst, cyclohexene technology, applied to oxide or hydroxide catalysts, including metal fields, can solve problems such as difficult retention, and achieve long life, good selectivity, and high activity.
- Summary
- Abstract
- Description
- Claims
- Application Information
AI Technical Summary
Problems solved by technology
Method used
Examples
Embodiment 1
[0052] Put 2.7g of ruthenium chloride and 0.022g of lanthanum chloride in a 1000ml beaker, add 200ml of deionized water and stir to dissolve to obtain solution 1.
[0053] Add 9.0 g of zirconium dioxide into solution 1 and continue stirring for 30 minutes to obtain emulsion 2.
[0054] At 20°C, 2.7g of sodium borohydride was dissolved in 50ml of distilled water, and added dropwise to emulsion 2, and the emulsion changed from milky white to brown, brown, and black in turn. After the dropwise addition was completed, the stirring was stopped to obtain a cloudy solution 3, which was left to stand and separated into layers.
[0055] The supernatant in 3 was decanted, and the black solid in the lower layer was retained. Wash with deionized water several times in small amounts. 0.01mol / L silver nitrate solution was used to test the chlorine ions in the washing solution until no white precipitate was formed to obtain 10 g of supported amorphous alloy catalyst.
[0056] In the catal...
Embodiment 2
[0058] Put 4.1g of ruthenium chloride and 0.18g of lanthanum chloride in a 1000ml beaker, add 300ml of deionized water and stir to dissolve to obtain solution 1.
[0059] Add 8.5 g of zirconium dioxide to solution 1, and continue stirring for 40 minutes to obtain emulsion 2.
[0060] At 25°C, 10.2g of sodium borohydride was dissolved in 150ml of distilled water, and added dropwise to emulsion 2, and the emulsion changed from milky white to brown, brown, and black in turn. After the dropwise addition was completed, the stirring was stopped to obtain a cloudy solution 3, which was left to stand and separated into layers.
[0061] The supernatant in 3 was decanted, and the black solid in the lower layer was retained. Wash with deionized water several times in small amounts. 0.01mol / L silver nitrate solution was used to test the chlorine ions in the washing solution until no white precipitate was formed to obtain 10 g of supported amorphous alloy catalyst.
[0062] In the catal...
Embodiment 3
[0064] Put 5 g of ruthenium chloride and 0.35 g of lanthanum chloride in a 1000 ml beaker, add 300 ml of deionized water and stir to dissolve, to obtain solution 1.
[0065] Add 9g of zirconium dioxide into solution 1, and continue to stir for 40 minutes to obtain emulsion 2.
[0066] At 25°C, 15g of sodium borohydride was dissolved in 180ml of distilled water, and added dropwise to emulsion 2, and the emulsion changed from milky white to brown, brown, and black in turn. After the dropwise addition was completed, the stirring was stopped to obtain a cloudy solution 3, which was left to stand and separated into layers.
[0067] The supernatant in 3 was decanted, and the black solid in the lower layer was retained. Wash with deionized water several times in small amounts. Chloride ions in the washing solution were tested with 0.01mol / L silver nitrate solution until no white precipitate was formed, and 11 g of the supported amorphous alloy catalyst was obtained.
[0068] In th...
PUM
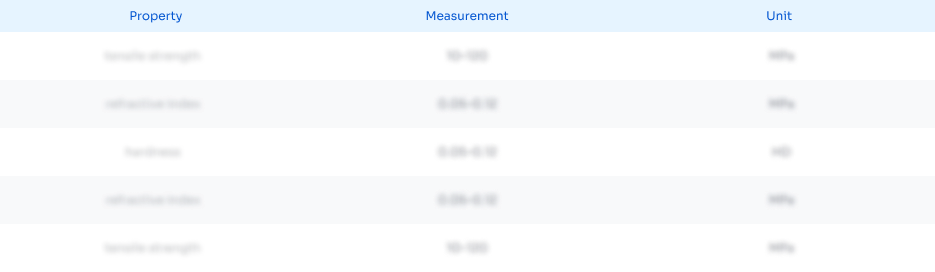
Abstract
Description
Claims
Application Information

- Generate Ideas
- Intellectual Property
- Life Sciences
- Materials
- Tech Scout
- Unparalleled Data Quality
- Higher Quality Content
- 60% Fewer Hallucinations
Browse by: Latest US Patents, China's latest patents, Technical Efficacy Thesaurus, Application Domain, Technology Topic, Popular Technical Reports.
© 2025 PatSnap. All rights reserved.Legal|Privacy policy|Modern Slavery Act Transparency Statement|Sitemap|About US| Contact US: help@patsnap.com