Integral turbine orientated crystallization method
A directional crystallization and turbine technology, applied in the field of casting, can solve the problems of fine grains in key areas, failure to meet requirements, and high probability of turbine flying cracks.
- Summary
- Abstract
- Description
- Claims
- Application Information
AI Technical Summary
Problems solved by technology
Method used
Image
Examples
Embodiment Construction
[0013] 1. Cladding: In order to strictly control the direction of heat flow during the solidification process of the alloy, so that the alloy liquid will always solidify along the expected direction, we wrap 1-10 mm of thermal insulation material 3 on the plane of the turbine big-end formwork 2, as shown in 2 As shown in the figure; 1 of them is the gating system.
[0014] 2. Box filling with sand: In order to form an effective temperature gradient at the solidification interface of the alloy, ensure that the metal grains at the blade grow toward the liquid phase along the direction opposite to the heat flow, and obtain oriented columnar crystals, use quartz sand outside the mold shell 5 filling, with insulation board 4 on the upper and lower sides. The specific method is shown in Figure 3;
[0015] 3. Roasting: In order to burn off volatile matter and moisture, increase the strength of the mold shell, and reduce the temperature difference when the molten metal is poured, the...
PUM
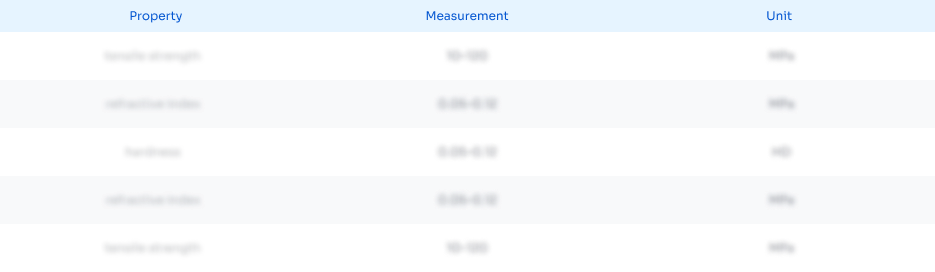
Abstract
Description
Claims
Application Information

- Generate Ideas
- Intellectual Property
- Life Sciences
- Materials
- Tech Scout
- Unparalleled Data Quality
- Higher Quality Content
- 60% Fewer Hallucinations
Browse by: Latest US Patents, China's latest patents, Technical Efficacy Thesaurus, Application Domain, Technology Topic, Popular Technical Reports.
© 2025 PatSnap. All rights reserved.Legal|Privacy policy|Modern Slavery Act Transparency Statement|Sitemap|About US| Contact US: help@patsnap.com