Light composite base material board and its manufacturing method
A composite base material and manufacturing method technology, applied in the direction of manufacturing tools, building materials, ceramic molding machines, etc., can solve the problems of low productivity, stimulation, and long demoulding time, and achieve easy implementation, high strength, and use Wide range of effects
- Summary
- Abstract
- Description
- Claims
- Application Information
AI Technical Summary
Problems solved by technology
Method used
Image
Examples
Embodiment 1
[0039] Embodiment 1: Composite adhesive preparation
[0040] Prepare composite adhesive: heat 100 parts by volume of No. 1807 glue (produced by Guangdong Jinwande Adhesive Products Co., Ltd., water-soluble, formaldehyde-free, environmentally friendly, the same below) to 60°C under normal pressure, and add while stirring 25 parts of polyvinyl acetate emulsion, stir evenly.
Embodiment 2
[0041] Embodiment 2: Manufacture of lightweight composite substrate board
[0042] A. Prepare composite adhesive: Heat 20 parts of No. 1807 glue by volume to 60°C under normal pressure, add 5 parts of polyvinyl acetate emulsion while stirring, and stir evenly;
[0043] B. Filler preparation: 30 parts by volume of cement, 75 parts of chaff and 55 parts of sawdust are fully stirred evenly;
[0044] C. Raw material preparation: the prepared filler and the prepared composite adhesive are fully stirred evenly,
[0045] D. Substrate molding: The prepared raw materials are put into the molding mold, flattened, slightly shaken, and compacted;
[0046] E. Mold removal and maintenance: Under normal pressure and temperature, let it stand for 2 days, remove the mold, trim the edge, and naturally maintain it for 10 days.
Embodiment 3
[0047] Embodiment 3: the manufacture of lightweight composite wallboard
[0048] A. Prepare composite adhesive: Heat 20 parts of No. 1807 glue by volume to 60°C under normal pressure, add 5 parts of polyvinyl acetate emulsion while stirring, and stir evenly;
[0049] B. Filler preparation: 30 parts by volume of cement, 75 parts of chaff and 55 parts of sawdust are fully stirred evenly;
[0050] C. Raw material preparation: the prepared filler and the prepared composite adhesive are fully stirred evenly,
[0051] D. Substrate molding: Before the raw materials are placed, pre-set reinforcing ribs in the forming mold. The reinforcing ribs are made of wood chips, and the prepared raw materials are placed in the forming mold, flattened, slightly shaken, and compacted;
[0052] E. Mold removal and maintenance: Under normal pressure and temperature, let it stand for 2 days, remove the mold, trim the edge, and naturally maintain it for 10 days.
PUM
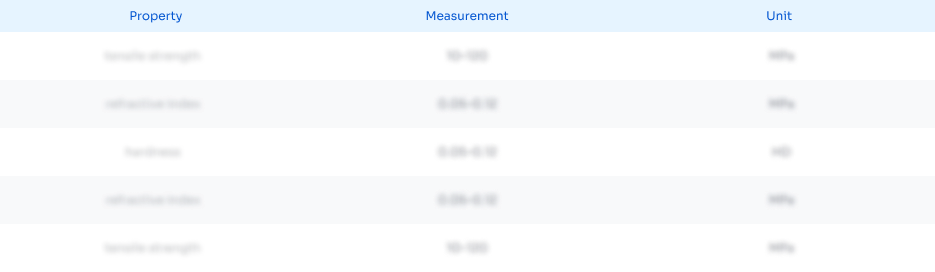
Abstract
Description
Claims
Application Information

- R&D
- Intellectual Property
- Life Sciences
- Materials
- Tech Scout
- Unparalleled Data Quality
- Higher Quality Content
- 60% Fewer Hallucinations
Browse by: Latest US Patents, China's latest patents, Technical Efficacy Thesaurus, Application Domain, Technology Topic, Popular Technical Reports.
© 2025 PatSnap. All rights reserved.Legal|Privacy policy|Modern Slavery Act Transparency Statement|Sitemap|About US| Contact US: help@patsnap.com