Silver-copper-carbon-rare earth alloy material and production thereof
A technology of rare earth alloys and alloy materials, applied in the field of material chemistry, can solve problems such as insufficient electrical conductivity, wear resistance and self-lubrication, and poor welding performance, and achieve poor electrical corrosion resistance, excellent performance, and obvious technical advantages Effect
- Summary
- Abstract
- Description
- Claims
- Application Information
AI Technical Summary
Problems solved by technology
Method used
Image
Examples
Embodiment 1
[0045] 1. Mixing: Weigh 10kg of Cu, 2kg of C, 0.1kg of rare earth, and 87.9kg of Ag for each component according to the formula, pass through an 80-mesh sieve after crushing, put into a mixing tank, and mix for 1 hour.
[0046] 2. Mechanical alloying reaction: Put the mixed powder into the material tank of the high-energy ball mill, put steel balls and grinding blocks with a volume three times the powder volume, seal the tank mouth, vacuumize to -0.1Mpa, and then Fill in 0.03Mpa nitrogen as a protective gas, turn on the cooling system and control system of the high-energy ball mill, and mechanically alloy for 5 hours; after the powder in the high-energy ball mill is cooled, take out the powder, pass through a 200-mesh sieve, and use a particle size smaller than 200 mesh Powder, the powder that cannot pass through the 200-mesh sieve is put back into the high-energy ball mill for crushing.
[0047] 3. Low-temperature annealing: using the existing technology, the powder prepared ...
Embodiment 2
[0055] 1. Mixing: Weigh 40kg of Cu, 10kg of C, 2.0kg of rare earth, and 48kg of Ag for each component according to the formula, pass through a 400-mesh sieve after crushing, put into a mixing tank, and mix for 3 hours.
[0056] 2. Mechanical alloying reaction: Put the mixed powder into the material tank of the high-energy ball mill, put steel balls and grinding blocks with a volume 5 times the powder volume, seal the tank mouth, vacuumize to -0.1Mpa, and then Fill in 0.03Mpa nitrogen as a protective gas, turn on the cooling system and control system of the high-energy ball mill, and mechanically alloy for 10 hours; after the powder in the high-energy ball mill is cooled, take out the powder and pass through a 200-mesh sieve.
[0057] 3. Low-temperature annealing: using the existing technology, the powder prepared in step 2 is subjected to low-temperature stress-relief annealing at a temperature of 500-550° C. with hydrogen as a protective gas, and the annealing time is 2 hours....
Embodiment 3
[0065] 1. Mixing: Weigh 25Kg of Cu, C3 Kg, 0.5 Kg of rare earth, and 71.5Kg of Ag for each component according to the formula, pass through a 200-mesh sieve after crushing, put into a mixing tank, and mix for 2.5 hours.
[0066] 2. Mechanical alloying reaction: put the mixed powder into the material tank of the high-energy ball mill, put steel balls and grinding blocks whose volume is 4 times the powder volume, seal the tank mouth, vacuumize to -0.1Mpa, and then Fill in 0.03Mpa nitrogen as a protective gas, turn on the cooling system and control system of the high-energy ball mill, and perform mechanical alloying for 7.5 hours; after the powder in the high-energy ball mill is cooled, take out the powder and pass through a 200-mesh sieve.
[0067] 3. Low-temperature annealing: the powder prepared in step 2 is subjected to low-temperature stress-relief annealing at a temperature of 500-550° C. using hydrogen as a protective gas, and the annealing time is 2 hours.
[0068] 4. Hot...
PUM
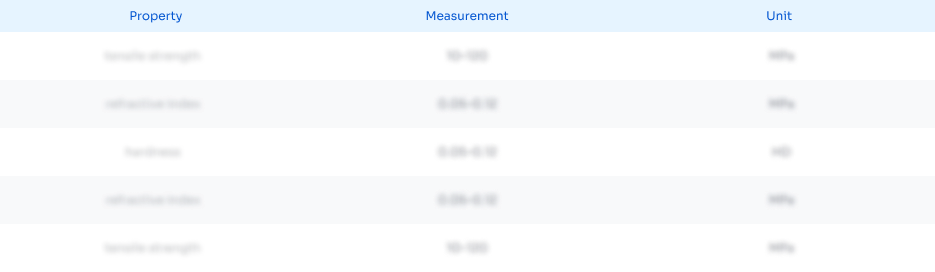
Abstract
Description
Claims
Application Information

- Generate Ideas
- Intellectual Property
- Life Sciences
- Materials
- Tech Scout
- Unparalleled Data Quality
- Higher Quality Content
- 60% Fewer Hallucinations
Browse by: Latest US Patents, China's latest patents, Technical Efficacy Thesaurus, Application Domain, Technology Topic, Popular Technical Reports.
© 2025 PatSnap. All rights reserved.Legal|Privacy policy|Modern Slavery Act Transparency Statement|Sitemap|About US| Contact US: help@patsnap.com