On-line silk screen printing process for paper production
A screen printing and process technology, applied in the field of online screen printing in paper production, can solve the problems of high power per unit area of equipment, inability to meet testing requirements, large water loss in paper, etc., to achieve high drying efficiency and shorten production. Cycle, the effect of less water loss
- Summary
- Abstract
- Description
- Claims
- Application Information
AI Technical Summary
Problems solved by technology
Method used
Examples
Embodiment Construction
[0032] The invention combines papermaking production with cylinder screen printing, performs online screen printing in the existing paper production process, and realizes online screen printing for continuous paper production. The specific process steps are as follows
[0033] pulping. Garden net papermaking forming. press. Pre-dry. For surface sizing, groove sizing, roller sizing or spraying can be used for surface sizing. The groove sizing process is simple and the cost is low. Air cushion drying, hot air drying can be used for drying, but UV curing is generally used, which has high drying efficiency, short drying time, less water loss for online paper production, and small footprint. Soft calendering. Moisture scan detection. Printing process: There are two links of printing and drying. Specifically, printing processes such as screen printing, offset printing, gravure printing or missing printing can be used. Carry out roll paper and put it into storage. Before roll...
PUM
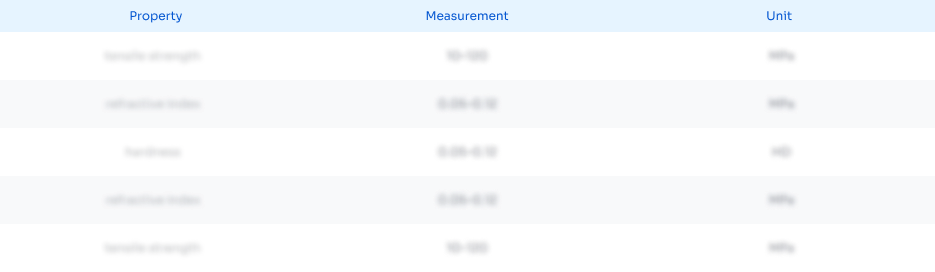
Abstract
Description
Claims
Application Information

- R&D Engineer
- R&D Manager
- IP Professional
- Industry Leading Data Capabilities
- Powerful AI technology
- Patent DNA Extraction
Browse by: Latest US Patents, China's latest patents, Technical Efficacy Thesaurus, Application Domain, Technology Topic, Popular Technical Reports.
© 2024 PatSnap. All rights reserved.Legal|Privacy policy|Modern Slavery Act Transparency Statement|Sitemap|About US| Contact US: help@patsnap.com