Drill and production method thereof
一种钻头、旋转方向的技术,应用在制造工具、修钻、麻花钻等方向,能够解决刀尖部1′刚性降低等问题
- Summary
- Abstract
- Description
- Claims
- Application Information
AI Technical Summary
Problems solved by technology
Method used
Image
Examples
Embodiment
[0151] for illustration Figure 11 to Figure 17 The effect of the drill bit shown will be based on the Figure 11 to Figure 17 Cutting tests were performed on the double-edged drill of the embodiment shown as an example, and the double-edged drill of the prior art as a prior art example. The results are shown in Figure 18 .
[0152] It can be seen that, in the embodiment as an example of the present invention, the roughness of the inner wall surface of the inlet portion and the outlet portion of the machining hole is well kept small, whereas in the prior art example, The roughness of the inner wall surface of the inlet part and the outlet part of the processing hole deteriorates.
[0153] Figure 19 to Figure 21 Another embodiment of the drill bit of the present invention is shown.
[0154] In the drill of this embodiment, the drill main body 201 is formed of a hard material such as cemented carbide and has a substantially cylindrical shape centered on the axis O, and it...
PUM
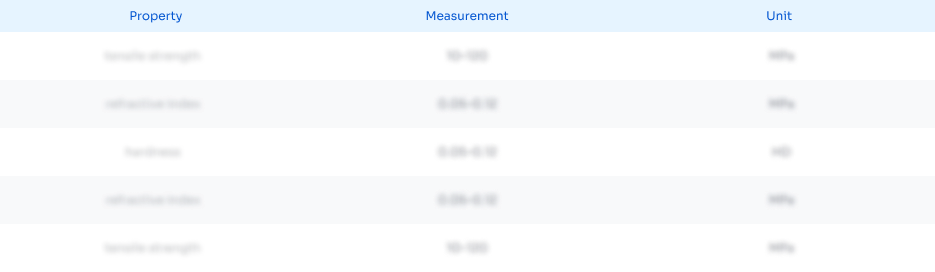
Abstract
Description
Claims
Application Information

- Generate Ideas
- Intellectual Property
- Life Sciences
- Materials
- Tech Scout
- Unparalleled Data Quality
- Higher Quality Content
- 60% Fewer Hallucinations
Browse by: Latest US Patents, China's latest patents, Technical Efficacy Thesaurus, Application Domain, Technology Topic, Popular Technical Reports.
© 2025 PatSnap. All rights reserved.Legal|Privacy policy|Modern Slavery Act Transparency Statement|Sitemap|About US| Contact US: help@patsnap.com