Superfine crystal particle hot-rolling steel plate with thick specification and production thereof
A technology of ultra-fine grain and hot-rolled steel plates, applied in metal rolling and other directions, can solve the problems of difficult process control, high price of alloy elements, high price, etc., and achieve the effect of good comprehensive performance, good cold bending performance and low cost
- Summary
- Abstract
- Description
- Claims
- Application Information
AI Technical Summary
Problems solved by technology
Method used
Examples
Embodiment 1
[0010] Converter smelting Q235 plain carbon steel, the chemical composition of steel includes: C: 0.13%, Si: 0.22%, Mn: 0.52%, P: 0.018%, S: 0.010%. The steel is cast into 200×(800~1200)×5500mm continuous casting slabs by conventional continuous casting methods, and the slabs are sent to a 1450mm hot continuous rolling mill for rolling. The whole process of heating, rolling and cooling is controlled. The rolling process control is as follows:
[0011] a. Control the continuous casting slab heating temperature to 1180°C; b. Rough rolling of the slab at 970°C, using six passes for rough rolling; c. The thickness of the intermediate slab after rough rolling is 31mm; d. Hot rolling and finishing rolling The inlet temperature is 890°C; e, the finishing rolling is carried out with six stands; f, the cooling water is put into three sets of stands; g, the exit temperature of hot rolling and finishing rolling is 810°C; h, the coiling temperature is 540°C.
[0012] The produced hot-rol...
Embodiment 2
[0014] Converter smelting Q235 plain carbon steel, the chemical composition of steel includes: C: 0.15%, Si: 0.25%, Mn: 0.61%, P: 0.015%, S: 0.008%. The steel is cast into 200×(800~1200)×5500mm continuous casting slabs by conventional continuous casting methods, and the slabs are sent to a 1450mm hot continuous rolling mill for rolling. The whole process of heating, rolling and cooling is controlled. The rolling process control is as follows:
[0015] a. Control the continuous casting slab heating temperature to 1200°C; b. Rough rolling of the slab at 980°C; c. The thickness of the intermediate slab after rough rolling is 34.5mm; d. The entrance temperature of hot rolling and finishing rolling is 910°C; e , Finish rolling is carried out with five stands; f, cooling water is put into four sets of stands; g, the exit temperature of hot rolling and finishing rolling is 830°C; h, the coiling temperature is 520°C.
[0016] The thickness of the produced hot-rolled steel plate is 7....
Embodiment 3
[0018] Converter smelting Q235 plain carbon steel, the chemical composition of steel includes: C: 0.17%, Si: 0.25%, Mn: 0.68%, P: 0.015%, S: 0.009%. The steel is cast into 200×(800~1200)×5500mm continuous casting slabs by conventional continuous casting methods, and the slabs are sent to a 1450mm hot continuous rolling mill for rolling, and the whole process of heating, rolling and cooling is controlled. The hot rolling process is controlled as follows:
[0019] a. Control the continuous casting slab heating temperature to 1200°C; b. Rough rolling of the slab at 980°C; c. The thickness of the intermediate slab after rough rolling is 35.5mm; d. The entrance temperature of hot rolling and finishing rolling is 920°C; e , Finish rolling is carried out with five stands; f, cooling water is put into four groups of stands; g, the exit temperature of hot rolling and finishing rolling is 830°C; h, the coiling temperature is 500°C.
[0020] The thickness of the produced hot-rolled stee...
PUM
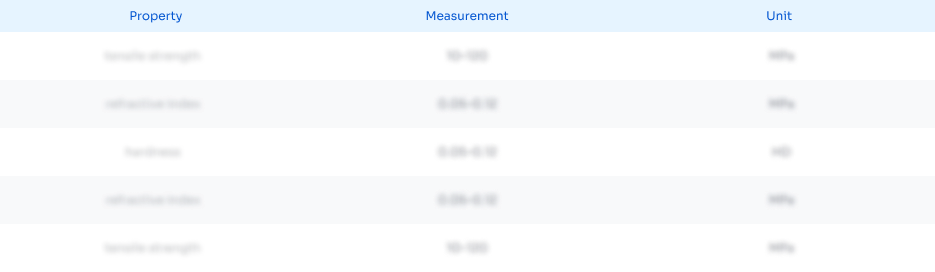
Abstract
Description
Claims
Application Information

- Generate Ideas
- Intellectual Property
- Life Sciences
- Materials
- Tech Scout
- Unparalleled Data Quality
- Higher Quality Content
- 60% Fewer Hallucinations
Browse by: Latest US Patents, China's latest patents, Technical Efficacy Thesaurus, Application Domain, Technology Topic, Popular Technical Reports.
© 2025 PatSnap. All rights reserved.Legal|Privacy policy|Modern Slavery Act Transparency Statement|Sitemap|About US| Contact US: help@patsnap.com