Vanadium niobium nitrogen melt and its production process
A technology of melt, vanadium and niobium, applied in the field of new multifunctional hybrid materials, can solve the problems of insufficient vanadium strengthening effect, unstable vanadium recovery rate, large addition amount, etc., to improve metallurgical reaction speed and metallurgical efficiency , The effect of reducing production costs
- Summary
- Abstract
- Description
- Claims
- Application Information
AI Technical Summary
Problems solved by technology
Method used
Examples
Embodiment 1
[0012] Embodiment 1 (according to total weight):
[0013] Grind 10% activated carbon, 3.5% titanium dioxide, 7% titanium nitride, 4% fluorite, 8% limestone, and niobium concentrate into 150-mesh fine powder in a container , fully stir and mix evenly, add 10% water glass to the container, mix evenly, mechanically shape, dry and pack for use.
Embodiment 2
[0014] Embodiment 2 (according to gross weight):
[0015] Grind 14% of ferrosilicon, 1.5% of aluminum, 14% of niobium nitride, 5.5% of fluorite, 12% of lime, and vanadium concentrate into 110-mesh fine powder in a container After stirring and mixing evenly, add 7% bitumen to the container, mix evenly, mechanically shape, dry and pack for use.
Embodiment 3
[0016] Embodiment 3 (according to total weight):
[0017] Grind 6% calcium silicon, 4% niobium nitride, 20% vanadium nitride, 2% bauxite, 3% dolomite and steelmaking vanadium slag into 190-mesh fine powder respectively Fully stir and mix in a container, then add 5% resin to the container, mix evenly, mechanically form, dry and pack for use.
PUM
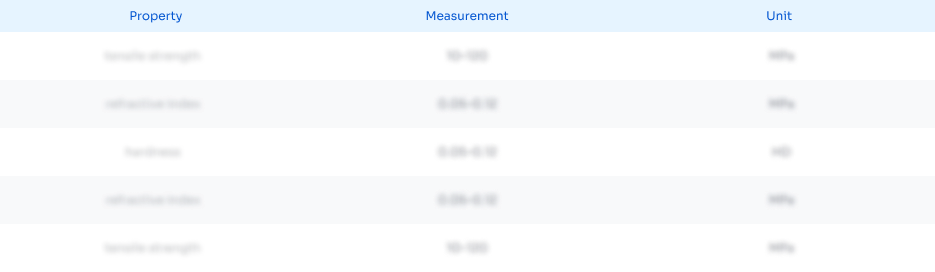
Abstract
Description
Claims
Application Information

- R&D
- Intellectual Property
- Life Sciences
- Materials
- Tech Scout
- Unparalleled Data Quality
- Higher Quality Content
- 60% Fewer Hallucinations
Browse by: Latest US Patents, China's latest patents, Technical Efficacy Thesaurus, Application Domain, Technology Topic, Popular Technical Reports.
© 2025 PatSnap. All rights reserved.Legal|Privacy policy|Modern Slavery Act Transparency Statement|Sitemap|About US| Contact US: help@patsnap.com