Thermal insulation energy-saving decoration tile and its making method
A manufacturing method and technology for decorative bricks, applied in the field of exterior wall decoration materials, can solve the problems of cumbersome construction procedures, poor EPS surface adhesion, and high construction costs, and achieve the effects of simple construction procedures, not easy to fall off, and low cost.
- Summary
- Abstract
- Description
- Claims
- Application Information
AI Technical Summary
Problems solved by technology
Method used
Image
Examples
Embodiment 1
[0010] Embodiment 1: by Figure 1-Figure 3 It can be seen that, by weight, the core material: formula: A material 1050 polyether 100, modifier, castor oil or glycerin 5-10, organotin 0.1-1.5, triethylamine (or triethanolamine) 1-3, water 2.0-3.5, silicone oil 0.5-3, B material isocyanate. Put each material in the above material A into the reaction kettle, stir and mix evenly (if it needs to be heated to 30°C+5° in winter), after about 30 minutes, input it into the material tank of the foaming machine. Input material B isocyanate into material tank B of the foaming machine, and keep the temperature of material tanks A and B constant for about 30 minutes after stirring, and keep the temperature between 35°C and 25°C depending on the weather conditions. Manufacture the core material according to the core material manufacturing process. A material and B material 0.5-1.0, leveling agent 1.0-5, antifungal agent 0.1-1.0, stone powder 350. Manufacture: according to the weight ratio...
Embodiment 2
[0011] Embodiment 2: core material: formula: A material: 835 polyether 100, modifier quantity castor oil or pentaerythritol 5-15, organotin 0.1-1.5 triethylamine (triethanolamine) 0.5-2.5, water 1.0-3.0, Silicone oil 0.5-2.0, B material: isocyanate, manufacture: the weight ratio of A material and B material is 1: 1.10-1.30, manufacture according to the manufacturing process of embodiment 1. Decorative coating: formula: pure acrylic emulsion 100, dispersant: 1-5, pigment: iron oxide red 8, defoamer: 0.5-5, leveling agent 0-3.5, antifungal agent 0.5-1.0, stone powder 350- 400. Manufacture: carry out by embodiment 1 manufacturing process. Manufacture of thermal insulation and energy-saving decorative bricks: carry out according to the manufacturing process of Example 1.
Embodiment 3
[0012] Embodiment 3: core material: formula, manufacture is the same as embodiment 1. Decorative coating: formula, manufacture with embodiment 1. Manufacture of thermal insulation and energy-saving decorative bricks: Take a piece of core material that has been cut, first scrape and coat 3-5mm cement slurry on its surface, and leave it for 12 to 24 hours to make the surface dry initially, then press 3kg / m 2 Place the decorative layer paint on the surface of the dried cement paste, scrape it with a scraper or spray it directly. After standing for 3 minutes, shake lightly for 1 minute to make the stone powder sink, and the surface is bright and smooth. Place it in a ventilated and dry place for drying and curing, and then it will be made into thermal insulation and energy-saving decorative bricks.
PUM
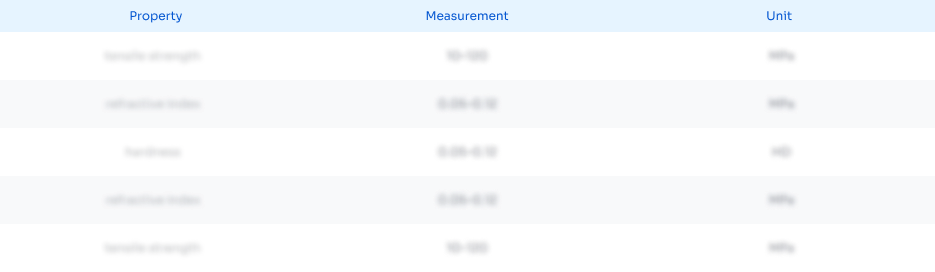
Abstract
Description
Claims
Application Information

- R&D Engineer
- R&D Manager
- IP Professional
- Industry Leading Data Capabilities
- Powerful AI technology
- Patent DNA Extraction
Browse by: Latest US Patents, China's latest patents, Technical Efficacy Thesaurus, Application Domain, Technology Topic, Popular Technical Reports.
© 2024 PatSnap. All rights reserved.Legal|Privacy policy|Modern Slavery Act Transparency Statement|Sitemap|About US| Contact US: help@patsnap.com