Treatment method for improving iron casting frozen tissue
A treatment method and solidification structure technology, which is applied in the field of improving the solidification structure of cast iron, can solve the problems of unsatisfactory temperature field and composition homogenization, insignificant refinement, and metal liquid pollution, etc., to achieve solidification Clear organization, simple and convenient process operation, energy saving effect
- Summary
- Abstract
- Description
- Claims
- Application Information
AI Technical Summary
Problems solved by technology
Method used
Examples
Embodiment 1
[0006] Example 1: Sand casting the molten iron into a cylindrical iron rod with a diameter of 50×200 mm. After pouring, pulse current treatment is performed on the molten iron during the solidification process until the solidification of the molten iron is completed.
[0007] The composition and content (weight percentage) of cast iron are: C 4.10%, Si 1.92%, Mn 0.22%, P0.058%, S 0.023%, Fe balance, the temperature at which the molten iron begins to be processed is 1250 ° C, when the temperature drops to When the temperature is 1000°C, the energization treatment is stopped; the process parameters are as follows: the pulse frequency is 0.8Hz, the output voltage U is 2000V, and the current intensity I is 30000A.
Embodiment 2
[0008] Embodiment 2: The test process is exactly the same as that of Embodiment 1, and the chemical composition and content (weight percent) of the cast iron are also the same. However, different process parameters are used. The process parameters are: pulse frequency 1000Hz, output voltage U is 50V, and current intensity I is 800A.
Embodiment 3
[0009] Example 3: The test process is exactly the same as Example 1. The composition and content (weight percentage) of cast iron are: C 3.58%, Si 1.60%, Mn 0.18%, P 0.045%, S 0.020%, Fe balance, iron The temperature at the beginning of the liquid treatment is 1250°C. When the temperature drops to 1000°C, the energization treatment is stopped; the process parameters are as follows: the pulse frequency is 0.1Hz, the output voltage U is 5000V, and the current intensity I is 100000A.
PUM
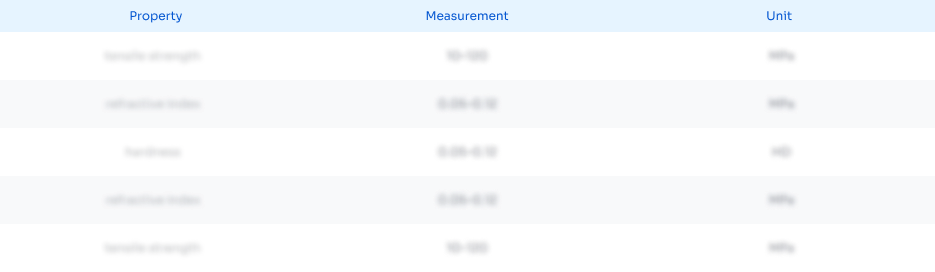
Abstract
Description
Claims
Application Information

- R&D
- Intellectual Property
- Life Sciences
- Materials
- Tech Scout
- Unparalleled Data Quality
- Higher Quality Content
- 60% Fewer Hallucinations
Browse by: Latest US Patents, China's latest patents, Technical Efficacy Thesaurus, Application Domain, Technology Topic, Popular Technical Reports.
© 2025 PatSnap. All rights reserved.Legal|Privacy policy|Modern Slavery Act Transparency Statement|Sitemap|About US| Contact US: help@patsnap.com