Process for alkylation of isoalkane and olefin
A technology of isoparaffin and alkylation reaction, which is applied in the field of addition of saturated hydrocarbons and unsaturated hydrocarbons, can solve problems such as impact on human body and ecological environment, pollution of ecological environment, corrosion of equipment and unsafe production operations, etc. Effect of Olefin Conversion
- Summary
- Abstract
- Description
- Claims
- Application Information
AI Technical Summary
Problems solved by technology
Method used
Examples
Embodiment 1
[0028] This example illustrates the nano-beta molecular sieve / SiO 2 preparation.
[0029] Dissolve 20.8 g of ethyl orthosilicate (produced by Beijing Chemical Reagent Company, analytically pure) in 5.76 g of absolute ethanol (Beijing Chemical Plant, analytically pure), and add it dropwise to 100 ml of 0.01M HCl under stirring to obtain silicon hydrolysis The final clarified sol (pH=2), then 28.8g of nano-beta molecular sieve slurry (molecular sieve concentration in the slurry is 38% by weight, adjust its pH=14 with 0.8M NaOH) is added to the above-mentioned silica sol under stirring, and the sol is A gel was formed within 10-20 seconds (the pH of the gel was measured to be 9 with precision pH test paper). The resulting gel was dried at 40° C. to obtain a composite xerogel containing 65% molecular sieve. Grind the product, sieve 40-60 mesh particles, beat and wash twice with hot water at 60°C, then exchange ammonium with 400ml of 1N ammonium chloride solution for 4 times, eac...
Embodiment 2
[0032] This example illustrates the nano-beta molecular sieve / SiO 2 preparation.
[0033] Add 3.84 g of nano-beta molecular sieve slurry (molecular sieve concentration in the slurry is 38% by weight, adjust its pH=13 with 0.8M NaOH) to 22.5 g of acidic inorganic silica sol (commercial product of Beijing Changhong Chemical Factory, SiO 2 The content is 25.9% by weight, pH=1.6), the sol forms a gel within 10-20 seconds (the pH of the gel is measured by precision pH test paper=7.5). The resulting gel was dried at 40° C. to obtain a composite xerogel containing 20% molecular sieve. Grind the product, sieve 40-60 mesh particles, beat and wash twice with hot water at 60°C, then exchange ammonium with 400ml of 1N ammonium chloride solution for 4 times, each time for 2 hours, and filter after each exchange , washing, and drying at 110° C. for 2 hours to obtain an ammonium-type product. Recorded as B2, SiO 2 The weight ratio to β molecular sieve is 4.
[0034] According to the m...
Embodiment 3
[0036] Description Nano Beta Molecular Sieve / Al 2 o 3 preparation.
[0037] 1.68g of nano-beta molecular sieve slurry JY (molecular sieve concentration in the slurry is 38% by weight, and its pH=13) is added to 7.3g of acidic aluminum sol (commercial product of Qilu Petrochemical Company Catalyst Factory, made by the reaction of metal aluminum and hydrochloric acid) under stirring. al 2 o 3 The content is 35% by weight, pH = 1.5), the sol rapidly forms a gel within 5-10s (the pH of the gel is measured by precision pH test paper = 8). The resulting gel was dried at 70°C to obtain a composite xerogel containing 65% molecular sieve. Grind the product, sieve 40-60 mesh particles, beat and wash twice with hot water at 60°C, then exchange ammonium with 400ml of 1N ammonium chloride solution for 4 times, each time for 2 hours, and filter after each exchange , washing, and drying at 110° C. for 2 hours to obtain an ammonium-type product. Recorded as B3, Al 2 o 3 The weight rat...
PUM
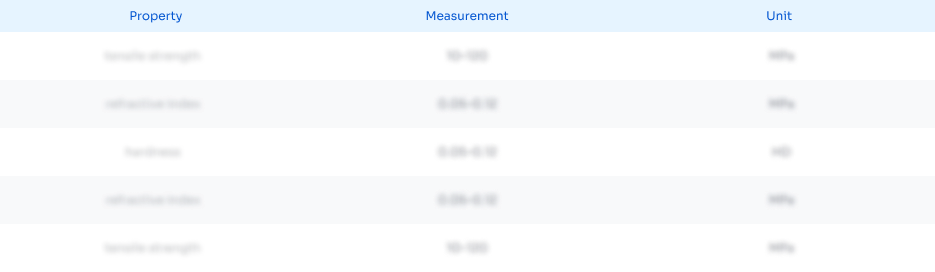
Abstract
Description
Claims
Application Information

- R&D
- Intellectual Property
- Life Sciences
- Materials
- Tech Scout
- Unparalleled Data Quality
- Higher Quality Content
- 60% Fewer Hallucinations
Browse by: Latest US Patents, China's latest patents, Technical Efficacy Thesaurus, Application Domain, Technology Topic, Popular Technical Reports.
© 2025 PatSnap. All rights reserved.Legal|Privacy policy|Modern Slavery Act Transparency Statement|Sitemap|About US| Contact US: help@patsnap.com