Composite heat sink semiconductor laser structure and its prepn. method
A semiconductor and laser technology, applied in the field of new composite heat sink high-power semiconductor laser array/stacked array structure and its preparation, can solve the problems of difficult welding process, high production cost, large thermal resistance of devices, etc., and achieve consistency Good, reduce the production cost, improve the effect of mechanical strength
- Summary
- Abstract
- Description
- Claims
- Application Information
AI Technical Summary
Problems solved by technology
Method used
Image
Examples
Embodiment 1
[0014] Embodiment 1: The structure of the present invention is shown in Figure e, which includes a laser chip bar 1, a high thermal conductivity conductive material 2, and a high thermal conductivity insulating material 3. Laser chip bar 1 adopts AlGaAs quantum well epitaxial wafer or InGaAsP quantum well epitaxial wafer or AlGaAsP quantum well epitaxial wafer, etc.; high thermal conductivity and electrical conductivity material 2 adopts oxygen-free copper or steel or aluminum; high thermal conductivity insulating material 3 adopts AlN ceramic or BeO ceramic or diamond etc.
Embodiment 2
[0015] Embodiment 2: preparation method of the present invention is as shown in figure a, b, c, d:
[0016] (1) Cut, polish, and clean oxygen-free copper, steel, aluminum, etc. as required to obtain a volume of 50×50×1.1mm 3 Oxygen-free copper or steel, aluminum and other rectangular blocks (as shown in Figure a).
[0017] (2) Cut and clean the surface of AlN ceramics or BeO ceramics, diamonds, etc. according to requirements, and then perform double-sided metallization treatment to obtain a volume of 50×50×0.2mm 3 Double-sided metallized AlN ceramics or BeO ceramics, diamond and other blocks (as shown in Figure b).
[0018] (3) Use Au / Sn solder paste or SnPb solder paste, heat-conducting glue, etc. to tightly weld the cut oxygen-free copper or steel, aluminum and other blocks with double-sided metallized AlN ceramics or BeO ceramics, and diamonds (adhesion) ) together to form a composite material (as shown in Figure c).
[0019] (4) Cut the composite material shown in Figur...
PUM
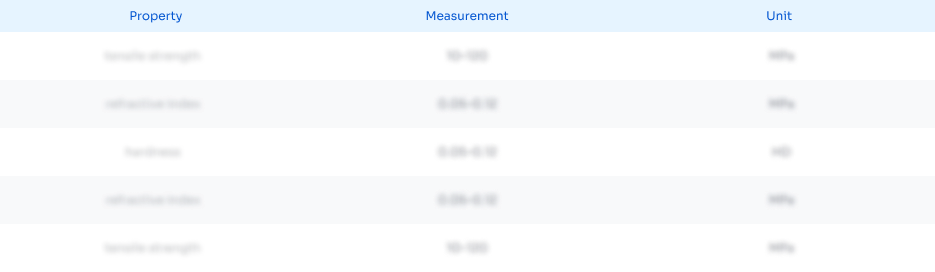
Abstract
Description
Claims
Application Information

- R&D Engineer
- R&D Manager
- IP Professional
- Industry Leading Data Capabilities
- Powerful AI technology
- Patent DNA Extraction
Browse by: Latest US Patents, China's latest patents, Technical Efficacy Thesaurus, Application Domain, Technology Topic, Popular Technical Reports.
© 2024 PatSnap. All rights reserved.Legal|Privacy policy|Modern Slavery Act Transparency Statement|Sitemap|About US| Contact US: help@patsnap.com