Composite mineralizer in use for calcinations of barium-copper cement
A mineralizer and cement technology, applied in the direction of cement production, etc., can solve the problems of no obvious effect on reducing energy consumption, inability to improve the flammability of raw materials, and inability to increase the output of kilns, etc., so as to reduce environmental pollution and equipment corrosion , shorten the firing time, and accelerate the solid-phase reaction speed
- Summary
- Abstract
- Description
- Claims
- Application Information
AI Technical Summary
Problems solved by technology
Method used
Examples
Embodiment Construction
[0016] The invention applies the barium-copper composite mineralizer to the process of making Portland cement. Specific embodiments and effects are as follows.
[0017] 1. The chemical composition of barium slag and copper slag used in this embodiment is shown in Table 1. Of course, the barium slag and copper slag of the present invention are not limited to the following chemical compositions.
[0018] Table 1: Chemical composition w% of barium slag and copper slag
[0019] Raw material Loss SiO 2 al 2 o 3 Fe 2 o 3 CaO MgO SO 3 BaO CuO
[0020] Barium dross 15.22 18.10 5.77 1.79 4.73 - 15.51 37.75
[0021] Copper slag -2.20 34.48 7.41 40.36 11.83 3.64 -- -- 0.7
[0022] 2. The chemical composition of cement raw meal and clinker used in this embodiment are shown in Table 2 and Table 3.
[0023] Table 2: Raw Meal Chemical Composition w%
[0024] Element
loss
SiO 2
Al 2 o 3
Fe 2 o 3
CaO
M...
PUM
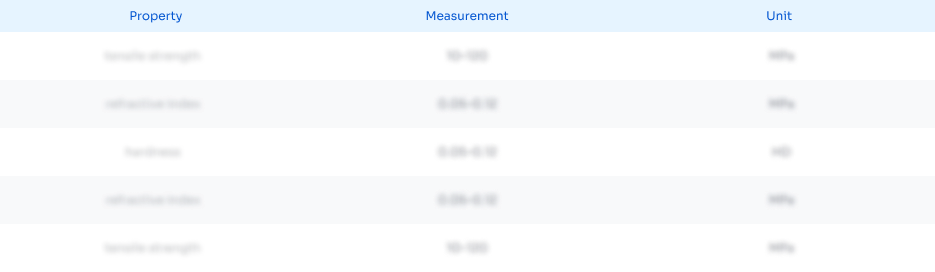
Abstract
Description
Claims
Application Information

- Generate Ideas
- Intellectual Property
- Life Sciences
- Materials
- Tech Scout
- Unparalleled Data Quality
- Higher Quality Content
- 60% Fewer Hallucinations
Browse by: Latest US Patents, China's latest patents, Technical Efficacy Thesaurus, Application Domain, Technology Topic, Popular Technical Reports.
© 2025 PatSnap. All rights reserved.Legal|Privacy policy|Modern Slavery Act Transparency Statement|Sitemap|About US| Contact US: help@patsnap.com