Method of manufacturing a matrix for a cathode-ray tube (CRT)
A substrate and electrode technology, applied in cathode ray tube/electron beam tube, cold cathode manufacturing, electrode system manufacturing, etc., can solve problems such as different sizes, misalignment, and inability to realize porous baffles
- Summary
- Abstract
- Description
- Claims
- Application Information
AI Technical Summary
Problems solved by technology
Method used
Image
Examples
Embodiment Construction
[0024] figure 1 A color cathode ray tube (CRT) 10 is shown having a glass envelope 11 comprising a face plate 12 and a neck 14 joined by a funnel 15 . The funnel 15 has an internal conductive coating (not shown) that contacts the anode button 16 and extends from the anode button 16 to the neck 14 .
[0025] Panel 12 includes a viewing panel 18 and a peripheral flange or side wall 20 sealed to funnel 15 by glass frit 21 . On the inner surface of the viewing panel 18 is carried a three-color fluorescent screen 22 . Such as figure 2 The screen 22 shown in cross-section in is a line screen, which includes a plurality of screen elements including red, green and blue fluorescent strips R, G and B arranged in triplets, respectively, Each triplet includes fluorescent lines for each of the three colors. The R, G and B fluorescent stripes are usually printed in a vertical direction.
[0026] Such as figure 2 The light absorbing matrix 23 is shown separating the fluorescent lines...
PUM
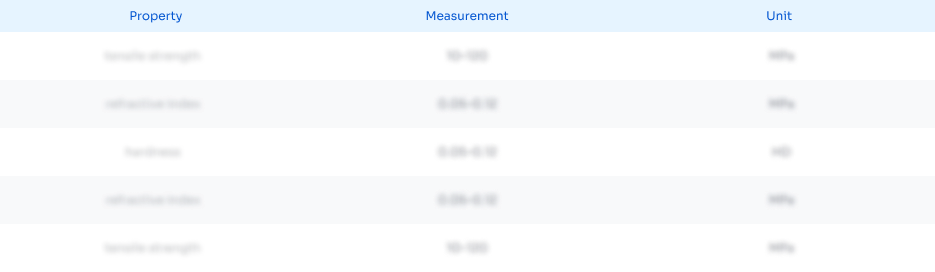
Abstract
Description
Claims
Application Information

- R&D Engineer
- R&D Manager
- IP Professional
- Industry Leading Data Capabilities
- Powerful AI technology
- Patent DNA Extraction
Browse by: Latest US Patents, China's latest patents, Technical Efficacy Thesaurus, Application Domain, Technology Topic.
© 2024 PatSnap. All rights reserved.Legal|Privacy policy|Modern Slavery Act Transparency Statement|Sitemap