Dynamic calcinator for inorganic material
A technology of dynamic calcination and inorganic materials, applied in furnaces, muffle furnaces, cooking furnaces, etc., can solve the problem that horizontal or vertical multi-stage fluidized calcination furnaces have not been widely used, cannot meet high-strength turning, and product quality is difficult Guarantee and other issues, to achieve the effect of solving fluidization quality problems, improving reliability, and uniform residence time
- Summary
- Abstract
- Description
- Claims
- Application Information
AI Technical Summary
Problems solved by technology
Method used
Image
Examples
Embodiment Construction
[0019] The present invention is described as follows in conjunction with accompanying drawing by embodiment:
[0020] figure 1 It is a structural representation of the present invention.
[0021] As shown in the figure, the shell 1, the heat insulation layer 2 and the refractory lining 3 constitute the furnace body. There are feeding ports 4 and smoke exhaust outlets 5 on the upper part of the furnace body and on one side of the furnace body. On the other side of the furnace body lower part There is a discharge port 6 on one side, and a burner nozzle 7 is arranged above the discharge port 6, and a burner nozzle 7 is fixed between one side of the furnace body and the other side of the furnace body, the discharge port 6 and the burner nozzle 7 below the feed port 4. Step-shaped gas distribution plate 8, a fluidized air distribution chamber 9 is fixed below the gas distribution plate 8, an agitator 10 is installed on the gas distribution plate 8, and an impeller feeder 11 is ins...
PUM
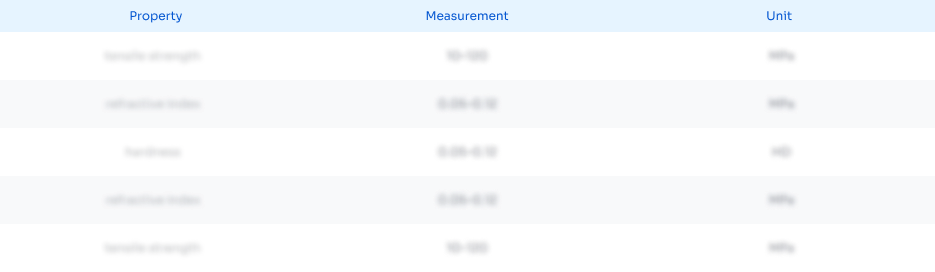
Abstract
Description
Claims
Application Information

- R&D Engineer
- R&D Manager
- IP Professional
- Industry Leading Data Capabilities
- Powerful AI technology
- Patent DNA Extraction
Browse by: Latest US Patents, China's latest patents, Technical Efficacy Thesaurus, Application Domain, Technology Topic, Popular Technical Reports.
© 2024 PatSnap. All rights reserved.Legal|Privacy policy|Modern Slavery Act Transparency Statement|Sitemap|About US| Contact US: help@patsnap.com