Preparation method of conductive polymer composite material possessing positive temperature coefficient characteristics
A technology of conductive polymer and positive temperature coefficient, applied in the field of preparation of conductive polymer composite materials, can solve the problems of lower percolation threshold, complicated operation process, inability to improve toughness, etc., and achieves good compatibility, simple operation process, Effect of changing switch temperature
- Summary
- Abstract
- Description
- Claims
- Application Information
AI Technical Summary
Problems solved by technology
Method used
Examples
Embodiment 1
[0022] (1) Treatment of conductive carbon black At room temperature, the polyisoprene rubber epoxy-modified aqueous emulsion is based on the dry rubber contained therein, and the ratio with carbon black is 4: 100, and the degree of epoxidation is 50% polyisoprene rubber epoxy-modified water-based emulsion is sprayed and dispersed on the surface of carbon black stirred at high speed. The amount of water is less than 0.1%;
[0023] (2) Preparation of conductive composite materials Put polyethylene pellets into a rubber-plastic internal mixer, at a speed of 25 to 35 rpm and a temperature of 170°C, after plasticizing for 4 minutes, press polyethylene and conductive carbon black The weight ratio is 100:15. Add the surface-treated carbon black into the high-temperature plasticized polyethylene and continue to knead for 6 minutes; take it out and cool it to room temperature, and use a plastic crusher to make a high-conductivity high Molecular composite pellets. The obtained granule...
Embodiment 2
[0025] (1) Treatment of conductive carbon black At room temperature, the polyisoprene rubber epoxy-modified aqueous emulsion is based on the dry rubber contained therein, and the ratio with carbon black is 20: 100, and the degree of epoxidation is 25% polyisoprene rubber epoxy-modified water-based emulsion is sprayed and dispersed on the surface of carbon black stirred at high speed. The amount of water is less than 0.1%;
[0026] (2) Preparation of conductive composite materials Put polyethylene pellets into a rubber-plastic internal mixer, at a speed of 25 to 35 rpm and a temperature of 220°C, after plasticizing for 3 minutes, press polyethylene and conductive carbon black The weight ratio of the carbon black is 100:40. Add the surface-treated carbon black into the high-temperature plasticized polyethylene and continue to knead for 10 minutes; take it out and cool it to room temperature, and use a plastic crusher to make a high-conductivity high-conductivity material with a ...
Embodiment 3
[0028] (1) Treatment of conductive carbon black At room temperature, the polyisoprene rubber epoxy-modified aqueous emulsion is based on the dry rubber contained therein, and the ratio with carbon black is 15: 100, and the degree of epoxidation is 15% polyisoprene rubber epoxy-modified water-based emulsion is sprayed and dispersed on the surface of carbon black stirred at high speed. The amount of water is less than 0.1%;
[0029] (2) Preparation of conductive composite materials Put polyethylene pellets into a rubber-plastic internal mixer, at a speed of 25 to 35 rpm and a temperature of 190°C, after plasticizing for 3 minutes, press polyethylene and conductive carbon black The weight ratio is 100:30. Add the surface-treated carbon black to the polyethylene that has been plasticized at high temperature, and continue to mix for 15 minutes; take it out and cool it to room temperature, and use a plastic crusher to make a high-conductivity high-conductivity material with positive...
PUM
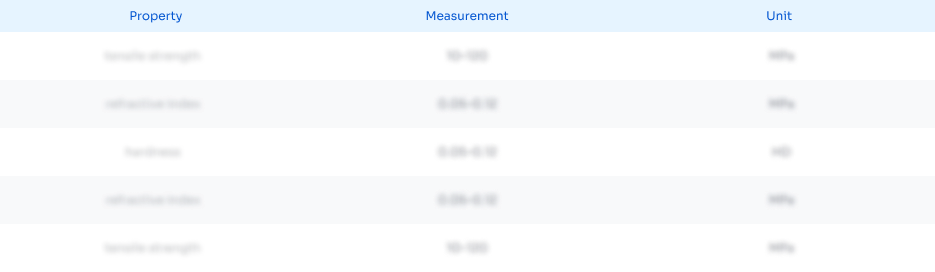
Abstract
Description
Claims
Application Information

- Generate Ideas
- Intellectual Property
- Life Sciences
- Materials
- Tech Scout
- Unparalleled Data Quality
- Higher Quality Content
- 60% Fewer Hallucinations
Browse by: Latest US Patents, China's latest patents, Technical Efficacy Thesaurus, Application Domain, Technology Topic, Popular Technical Reports.
© 2025 PatSnap. All rights reserved.Legal|Privacy policy|Modern Slavery Act Transparency Statement|Sitemap|About US| Contact US: help@patsnap.com