Production method of high purity aluminium scandium alloy
An aluminum-scandium and alloy technology is applied in the production field of high-purity aluminum-scandium alloy, which can solve the problems of long process, difficult operation and high cost, and achieve the effects of reducing production cost, improving metal recovery rate and improving quality.
- Summary
- Abstract
- Description
- Claims
- Application Information
AI Technical Summary
Problems solved by technology
Method used
Examples
Embodiment 1
[0020] The ratio of the control electrolyte is: aluminum fluoride AlF 3 25%, sodium fluoride NaF13%, barium chloride BaCl 2 57%, sodium chloride NaCl5%, add 15% scandium chloride ScCl in the electrolyte 3 . Its operating control parameters are: electrolysis temperature: 720°C, electrolytic cell working voltage: 4.5v, electrolyte thickness: 7.0cm. The chemical composition requirements of scandium chloride added to the electrolyte during electrolysis: scandium chloride ScCl 3 : >98.5%, loss on ignition <1%, sum of oxides <0.2%, sum of other impurities <0.3%. The weight percent chemical composition of the high-purity aluminum-scandium alloy produced by the method of the present invention is: scandium Sc 2.0%, the rest is aluminum Al and unavoidable impurities, wherein iron Fe<0.01%, silicon Si<0.01%, other impurities Sum < 0.02%.
Embodiment 2
[0022] The ratio of the control electrolyte is: aluminum fluoride AlF 3 22%, sodium fluoride NaF15%, barium chloride BaCl 2 55%, sodium chloride NaCl8%, add 1% scandium chloride ScCl in the electrolyte 3 . Its operating control parameters are: electrolysis temperature: 700°C, electrolytic cell working voltage: 5.0v, electrolyte thickness: 6.0cm. The chemical composition requirements of scandium chloride added to the electrolyte during electrolysis: scandium chloride ScCl 3 : >98.5%, loss on ignition <1%, sum of oxides <0.2%, sum of other impurities <0.3%. The weight percent chemical composition of the high-purity aluminum-scandium alloy produced by the method of the present invention is: scandium Sc 0.1%, the rest is aluminum Al and unavoidable impurities, wherein iron Fe<0.01%, silicon Si<0.01%, other impurities Sum < 0.02%.
Embodiment 3
[0024] The ratio of the control electrolyte is: aluminum fluoride AlF 3 27%, sodium fluoride NaF15%, barium chloride BaCl 2 50%, sodium chloride NaCl8%, add 10% scandium chloride ScCl in the electrolyte 3 . Its operating control parameters are: electrolysis temperature: 750°C, electrolytic cell working voltage: 6.0v, electrolyte thickness: 13cm. The chemical composition requirements of scandium chloride added to the electrolyte during electrolysis: scandium chloride ScCl 3 : >98.5%, loss on ignition <1%, sum of oxides <0.2%, sum of other impurities <0.3%. The weight percent chemical composition of the high-purity aluminum-scandium alloy produced by the method of the present invention is: scandium Sc 1.0%, the rest is aluminum Al and unavoidable impurities, wherein iron Fe<0.01%, silicon Si<0.01%, other impurities Sum < 0.02%.
PUM
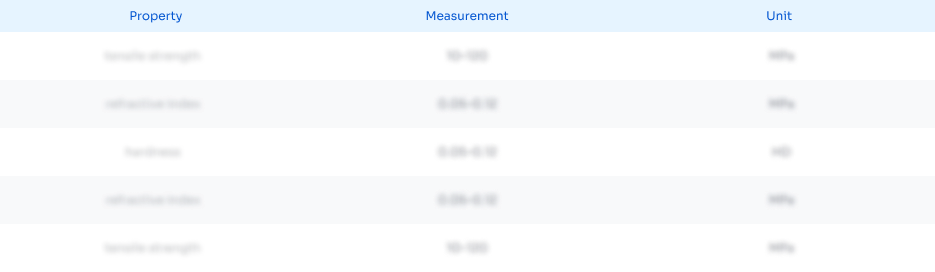
Abstract
Description
Claims
Application Information

- R&D Engineer
- R&D Manager
- IP Professional
- Industry Leading Data Capabilities
- Powerful AI technology
- Patent DNA Extraction
Browse by: Latest US Patents, China's latest patents, Technical Efficacy Thesaurus, Application Domain, Technology Topic, Popular Technical Reports.
© 2024 PatSnap. All rights reserved.Legal|Privacy policy|Modern Slavery Act Transparency Statement|Sitemap|About US| Contact US: help@patsnap.com