Production method of non alloy precooled isothermal bardening austenic globe body
A technology of austempering and production methods, which is applied in the production field of non-alloy precooling and austempering ausferitic ductile iron, to achieve the effect of ensuring safety and expanding the scope of application
- Summary
- Abstract
- Description
- Claims
- Application Information
AI Technical Summary
Problems solved by technology
Method used
Image
Examples
Embodiment 1
[0016] 1. Casting method:
[0017] The composition of the non-alloy precooling austempering austeric ductile iron is (weight percent):
[0018] C 3.55% Si 2.63% Mn 0.3%
[0019] P 0.05% S 0.012% Mg 0.035%
[0020] Rare earth element RE 0.02%
[0021] The rest is Fe
[0022] The conventional casting method is adopted, that is, pig iron, scrap steel, recycled materials, ferrosilicon, and ferromanganese are selected in different proportions to ensure the content of C, Si, and Mn, and low-phosphorus pig iron is selected to ensure the content of P, and low-S pig iron is selected. The S method ensures the S content, and selects the appropriate amount of nodulizer to ensure the RE and Mg content; the melting adopts a 0.5T intermediate frequency electric furnace, and according to the rapid detection results before the furnace, add carburant, pig iron, scrap steel, ferrosilicon, ferromanganese, etc. , the added alloy elements must be added into the furnace 10 minutes before the sph...
Embodiment 2
[0026] 1. Casting method:
[0027] The composition of the non-alloy precooling austempering austeric ductile iron is (weight percent):
[0028] C 3.6% Si 2.64% Mn 0.26%
[0029] P 0.04% S 0.010% Mg 0.035%
[0030] Rare earth elements RE 0.03%
[0031] The rest is Fe
[0032] Adopt conventional casting method, with embodiment one,
[0033] 2. Heat treatment method of castings
[0034] Heat the machined casting to 850°C in a trolley-type resistance furnace and keep it warm for 1.5 hours, then cool it to 790°C and keep it warm for 0.5 hours. When the oil is cooled to 250°C, it is transferred to an air isothermal furnace at 360°C, kept warm for 2 hours, then released from the furnace, and cooled in air.
Embodiment 3
[0036] 1. Casting method:
[0037] The composition of the non-alloy precooling austempering austeric ductile iron is (weight percent):
[0038] C 3.67% Si 2.69% Mn 0.40%
[0039] P 0.03% S 0.008% Mg 0.040%
[0040] Rare earth element RE 0.04%
[0041] The rest is Fe
[0042] Adopt conventional casting method, with embodiment one,
[0043] 2. Heat treatment method of castings
[0044] Heat the machined casting to 860°C in a trolley-type resistance furnace and keep it warm for 2 hours, then cool it to 790°C and keep it warm for 0.5 hours. When it is cooled to 260°C, the oil comes out, and it is transferred to an air isothermal furnace at 370°C, kept for 1.5 hours, then released from the furnace, and air-cooled.
PUM
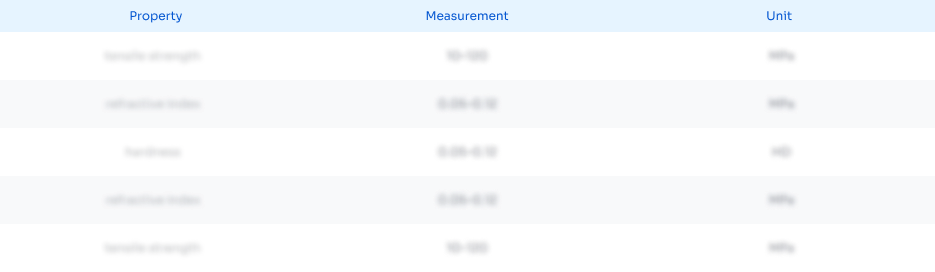
Abstract
Description
Claims
Application Information

- Generate Ideas
- Intellectual Property
- Life Sciences
- Materials
- Tech Scout
- Unparalleled Data Quality
- Higher Quality Content
- 60% Fewer Hallucinations
Browse by: Latest US Patents, China's latest patents, Technical Efficacy Thesaurus, Application Domain, Technology Topic, Popular Technical Reports.
© 2025 PatSnap. All rights reserved.Legal|Privacy policy|Modern Slavery Act Transparency Statement|Sitemap|About US| Contact US: help@patsnap.com