Resin size used for chip resistor
A resin paste and resistor technology, applied in the direction of resistor shell/packaging shell/potting, filling paste, epoxy resin glue, etc., can solve problems such as resistance value drift
- Summary
- Abstract
- Description
- Claims
- Application Information
AI Technical Summary
Problems solved by technology
Method used
Image
Examples
Embodiment Construction
[0016] Now in conjunction with table 2 and table 3 illustrate the most preferred embodiment of the present invention, in table 2, the thermosetting or thermoplastic resin that embodiment 1,2,7,8,13,14 adopts is polyvinyl butyral resin, black Fillers are pigmented carbon black and Al 2 o 3 It is prepared by mixing at a weight ratio of 1:4, and the white filler is TiO 2 and CaCO 3 Prepared by mixing at a weight ratio of 1:2; the thermosetting or thermoplastic resins used in Examples 3, 4, 9, 10, 15, and 16 are silicone resins, and the black filler is pigment carbon black and SiO 2 It is prepared by mixing at a weight ratio of 1:4, and the white filler is TiO 2 and Al 2 o 3 It is prepared by mixing in a weight ratio of 1: 2; the thermosetting or thermoplastic resin used in embodiments 5, 11, and 17 is an amino resin, and the black filler is prepared by mixing pigment carbon black and talcum powder in a weight ratio of 1: 4, The white filler is TiO 2 and SiO 2 Prepared by ...
PUM
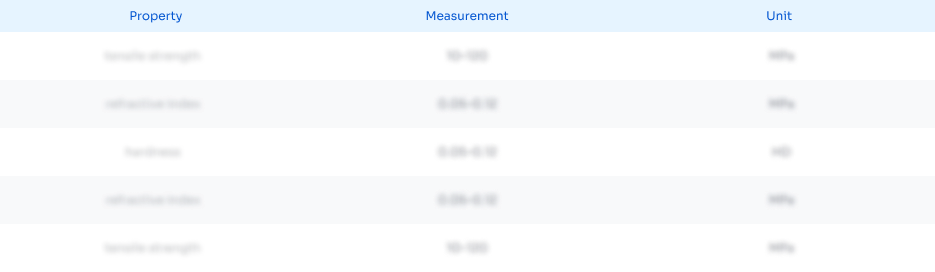
Abstract
Description
Claims
Application Information

- R&D
- Intellectual Property
- Life Sciences
- Materials
- Tech Scout
- Unparalleled Data Quality
- Higher Quality Content
- 60% Fewer Hallucinations
Browse by: Latest US Patents, China's latest patents, Technical Efficacy Thesaurus, Application Domain, Technology Topic, Popular Technical Reports.
© 2025 PatSnap. All rights reserved.Legal|Privacy policy|Modern Slavery Act Transparency Statement|Sitemap|About US| Contact US: help@patsnap.com