Leaching process of zinc oxide ore
A zinc oxide ore and leaching technology, which is applied in the field of hydrometallurgy, can solve the problems of uneconomical, increased consumption of neutralizer and sulfuric acid, and large loss of zinc with slag, so as to avoid consumption and increase the leaching rate.
- Summary
- Abstract
- Description
- Claims
- Application Information
AI Technical Summary
Problems solved by technology
Method used
Examples
Embodiment 1
[0012] Example 1: Select zinc oxide ore, its chemical composition is Zn26.55%, Fe18.20%, SiO 2 7.94%, of which zinc phase components are 24.23% zinc carbonate, 1.25% zinc silicate, 0.73% zinc sulfide, and 0.34% iron-zinc spinel. After the minerals are crushed and ground, they are neutrally leached with waste electrolyte. That is, the condition is that the initial value is PH3, the end point is PH5.2, and the uniform stirring is for 120-180 minutes; solid-liquid separation is carried out, the leaching liquid is used for electrolysis, and sulfuric acid solution is added to the leaching residue for low-acid leaching. The pH value starts from The PH5.2 gradually drops to PH1.5, then solid-liquid separation, and the supernatant is returned to the neutral leaching section for recycling. The main indicators are as follows:
[0013] Zinc leaching recovery rate: 91.88%
[0014] Cadmium leaching recovery rate: 95.86%
[0015] Slag rate: 55.45%
[0016] Zinc in slag: 3.89%
[0017] Slag filt...
Embodiment 2
[0018] Example 2: Select high-silicon zinc oxide ore, its chemical composition is Zn21.68%, Fe17.95%, SiO 2 18.91%, CaO6.65%, as in the above example, after crushing and pulverizing the minerals, use waste electrolyte for neutral leaching, that is, the initial value is PH3, the end point is PH5.2, and the uniform stirring is carried out for 120-180 minutes; Solid-liquid separation, the leaching liquid is used for electrolysis, adding sulfuric acid solution to the leaching residue for low-acid leaching, the PH value gradually drops from the initial PH5.2 to PH2.0, and then solid-liquid separation, the supernatant returns to neutral The leaching section is recycled. The main indicators are as follows:
[0019] Zinc leaching recovery rate: 89.7%
[0020] Filtration speed of acid leaching pulp: 606.2L / m 2 h
[0021] Slag rate: 64.5%
[0022] Zinc content in slag: 3.46%
Embodiment 3
[0023] Example 3: Select zinc oxide concentrate, the chemical composition of which is Zn26.55%, Fe18.20%, SiO 2 7.94%, of which zinc phase components are 24.23% zinc carbonate, 1.25% zinc silicate, 0.73% zinc sulfide, and 0.34% iron-zinc spinel. After the minerals are crushed and ground, they are neutrally leached with waste electrolyte. That is, the condition is that the initial value is PH3, the end point is PH5.2, and the uniform stirring is for 120-180 minutes; solid-liquid separation is carried out, the leaching liquid is used for electrolysis, and sulfuric acid solution is added to the leaching residue for low-acid leaching. The pH value starts from The PH5.2 gradually drops to PH1.5, then solid-liquid separation, and the supernatant is returned to the neutral leaching section for recycling. The main indicators are as follows:
[0024] Zinc leaching recovery rate: 91.88%
[0025] Cadmium leaching recovery rate: 95.86%
[0026] Slag rate: 55.45%
[0027] Zinc in slag: 3.89%
...
PUM
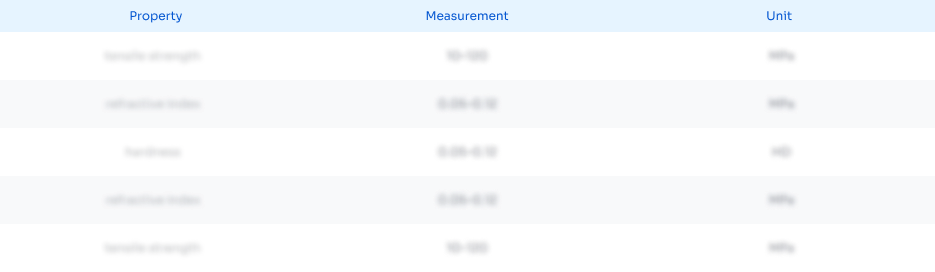
Abstract
Description
Claims
Application Information

- R&D Engineer
- R&D Manager
- IP Professional
- Industry Leading Data Capabilities
- Powerful AI technology
- Patent DNA Extraction
Browse by: Latest US Patents, China's latest patents, Technical Efficacy Thesaurus, Application Domain, Technology Topic, Popular Technical Reports.
© 2024 PatSnap. All rights reserved.Legal|Privacy policy|Modern Slavery Act Transparency Statement|Sitemap|About US| Contact US: help@patsnap.com