Image sensor packaging method
A technology of image sensors and circuit substrates, applied in the direction of electric solid-state devices, semiconductor devices, radiation control devices, etc., can solve problems such as warping of grains or products, peeling of two-layer PCB boards, poor product reliability, etc., and achieve packaging volume The effect of reducing and simplifying mechanical equipment and improving product reliability
- Summary
- Abstract
- Description
- Claims
- Application Information
AI Technical Summary
Problems solved by technology
Method used
Image
Examples
Embodiment Construction
[0042] Cooperate Figure 1 to Figure 8 Shown illustrates the flow process of the image sensor packaging method of the present invention, including:
[0043] Step 1: If figure 1 , figure 2 As shown, a window 12 is opened on the surface of a PCB circuit substrate 10 with a conductive layer 11 on one surface, and the window penetrates to another corresponding surface of the PCB circuit substrate. The size of the window is close to the size of the sensing area of an image sensor (such as Figure 5 21), and the walls of the window are coated with a shield 121 such as a solder mask or a gold-plated cover to prevent the dust after substrate processing from falling onto the surface of the image sensor die.
[0044] Step 2: If image 3 As shown, the aforementioned PCB circuit substrate is subjected to photomask etching (Etching) so that the conductive layer forms a plurality of leads (Leads) 110 on the window side, and each lead is set to include two parts: an inner lead 110a and ...
PUM
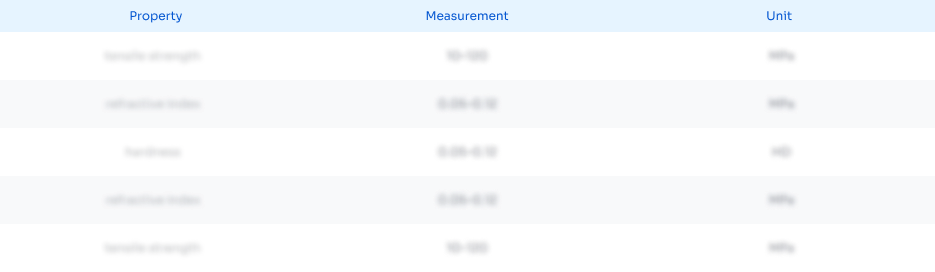
Abstract
Description
Claims
Application Information

- R&D Engineer
- R&D Manager
- IP Professional
- Industry Leading Data Capabilities
- Powerful AI technology
- Patent DNA Extraction
Browse by: Latest US Patents, China's latest patents, Technical Efficacy Thesaurus, Application Domain, Technology Topic, Popular Technical Reports.
© 2024 PatSnap. All rights reserved.Legal|Privacy policy|Modern Slavery Act Transparency Statement|Sitemap|About US| Contact US: help@patsnap.com