Suspension bed hydrogenation catalyst dispersion process
A hydrogenation catalyst and catalyst technology, applied in the direction of naphtha catalytic reforming, etc., can solve the problems of large particles, low yield of light oil, uneven dispersion, etc., achieve large surface area, large hydrogenation activity, and avoid coke formation. Effect
- Summary
- Abstract
- Description
- Claims
- Application Information
AI Technical Summary
Problems solved by technology
Method used
Examples
Embodiment 1
[0020] Put the container containing 500 grams of residual oil on a magnetic stirrer and heat it to 90°C, add 0.3 grams of T-80, 0.1 gram of n-hexanol and 17.3 grams of catalyst aqueous solution with a metal concentration of 0.866m%, and stir at a constant temperature of 90°C for 4 Hours, a homogeneously mixed raw material was obtained. Take 200 grams of the above-mentioned raw materials and put them into an autoclave. The autoclave is heated at a rate of 30°C / min, and is vulcanized at a constant temperature of 250°C and 350°C for half an hour. At the end of the constant temperature vulcanization at 350°C, samples are taken to analyze the dispersion of the catalyst. Then the temperature is raised to the reaction temperature, and the hydrocracking reaction is carried out under the reaction pressure.
Embodiment 2
[0022] Add 500 grams of 80°C residual oil raw material to a GYJ-type homogenizer, add 0.2 grams of T-85, 0.4 grams of n-amyl alcohol and 25 grams of a catalyst solution with a metal concentration of 0.3m%, and emulsify at a constant temperature of 80°C for 4 hours. A uniformly mixed raw material is obtained. Take 200 grams of the above-mentioned raw materials and put them into an autoclave. The autoclave is heated at a rate of 30°C / min, and is vulcanized at a constant temperature of 250°C and 350°C for half an hour. At the end of the constant temperature vulcanization at 350°C, samples are taken to analyze the dispersion of the catalyst. Then the temperature is raised to the reaction temperature, and the hydrocracking reaction is carried out under the reaction pressure.
Embodiment 3
[0024] Add 500 grams of residual oil at 80°C to an L50 vertical colloid mill, add 0.3 grams of NP-7, 0.2 grams of n-pentyl ether and 25 grams of an aqueous catalyst solution with a metal concentration of 0.1m%, and emulsify at a constant temperature of 80°C for 4 hours , to obtain uniformly mixed raw materials, take 200 grams of the above-mentioned raw materials and add them to the autoclave, the autoclave is heated at a rate of 30°C / min, and is vulcanized at a constant temperature of 250°C and 350°C for half an hour, and samples are taken at the end of the constant temperature vulcanization at 350°C. Used to analyze catalyst dispersion. Then the temperature is raised to the reaction temperature, and the hydrocracking reaction is carried out under the reaction pressure.
PUM
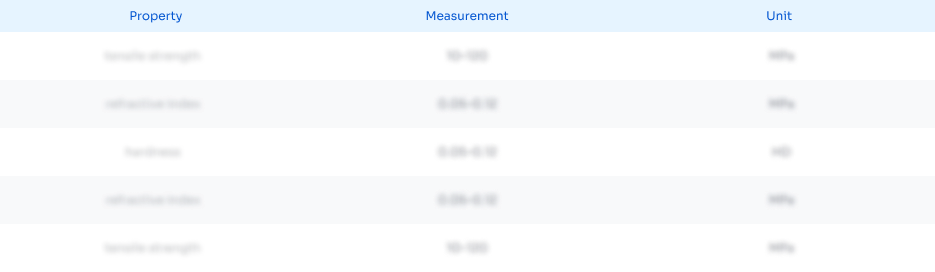
Abstract
Description
Claims
Application Information

- R&D
- Intellectual Property
- Life Sciences
- Materials
- Tech Scout
- Unparalleled Data Quality
- Higher Quality Content
- 60% Fewer Hallucinations
Browse by: Latest US Patents, China's latest patents, Technical Efficacy Thesaurus, Application Domain, Technology Topic, Popular Technical Reports.
© 2025 PatSnap. All rights reserved.Legal|Privacy policy|Modern Slavery Act Transparency Statement|Sitemap|About US| Contact US: help@patsnap.com