Semi-continuous process for preapring organofluorine polymer grafted polyether polyol
A technology of polyether polyol and grafted polyether, which is applied in the field of semi-continuous preparation of organic fluorine polymer and polyether polyol graft copolymer, can solve the problem of poor adhesion of fluorocarbon paint, wide polymer molecular weight distribution, Low monomer conversion rate and other problems, to achieve the effect of excellent weather resistance and strong adhesion
- Summary
- Abstract
- Description
- Claims
- Application Information
AI Technical Summary
Problems solved by technology
Method used
Examples
Embodiment 1
[0042] (a): Mixing kettle: 268g of vinyl acetate, 16g of undecylenic acid, 117g of unsaturated polyether polyol macromer I, 13g of initiator AIBN, and molecular weight regulator n-C 12 Add SH 4g into a mixing kettle equipped with a temperature controller and an electric stirrer with an effective volume of 1 liter, mix well and control the temperature at 10-15°C.
[0043] (b) Polymerization reactor: Add solvents such as xylene 350g and methyl isobutyl ketone 150g respectively to a pressure-resistant stainless steel polymerization reactor with a temperature controller, nitrogen protection, and an electric stirrer with an effective volume of 2 liters, nitrogen Replace three times, control the oxygen content to less than 60ppm, and raise the temperature to 72±2°C.
[0044] (c) Continuous feeding: The materials in 1 mixing tank are fed into the polymerization at the feed rate (mass) of 52.2g / hour and the feed liquid CTFE of 2 organofluorine monomers is 75g / hour respectively. In th...
Embodiment 2:(C)“CTFE75g/”“TFE65g/”, Embodiment 1。1。 Embodiment 3
[0047] (a): Mixing kettle: 185g of vinyl acetate, 16g of undecylenic acid, 200g of unsaturated polyether polyol macromer II, 13g of initiator AIBN, and molecular weight regulator n-C 12 Add SH4g into a mixing kettle equipped with a temperature controller and an electric stirrer with an effective volume of 1 liter, mix well and control the temperature at 10-15°C.
[0048] (b) Polymerization reactor: Add solvents such as xylene 350g and methyl isobutyl ketone 150g respectively to a pressure-resistant stainless steel polymerization reactor with a temperature controller, nitrogen protection, and an electric stirrer with an effective volume of 2 liters, nitrogen Replace three times, control the oxygen content to be less than ppm, and raise the temperature to 72±2°C.
[0049] (c) Continuous feeding: The materials in 1 mixing tank are fed into the polymerization at the feed rate (mass) of 52.2g / hour and the feed liquid CTFE of 2 organofluorine monomers is 75g / hour respectively. In t...
Embodiment 4
[0052] Embodiment 4: except that "CTFE is with the feed rate of 75g / hour" in (C) is changed into " TFE with the feed rate of 65g / hour ", all the other are the same as embodiment 3. The properties of the organic fluoropolymer grafted polyether polyol after drying are shown in Table 1.
PUM
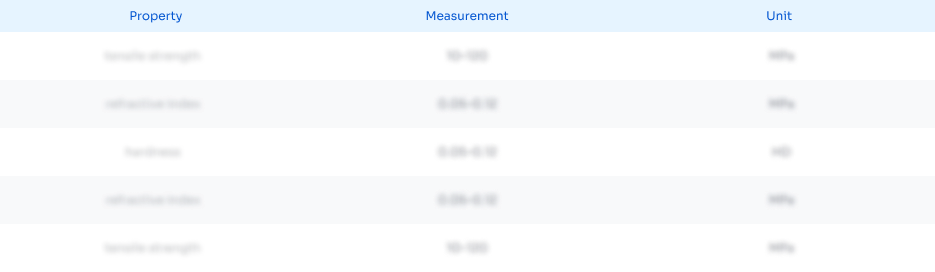
Abstract
Description
Claims
Application Information

- R&D
- Intellectual Property
- Life Sciences
- Materials
- Tech Scout
- Unparalleled Data Quality
- Higher Quality Content
- 60% Fewer Hallucinations
Browse by: Latest US Patents, China's latest patents, Technical Efficacy Thesaurus, Application Domain, Technology Topic, Popular Technical Reports.
© 2025 PatSnap. All rights reserved.Legal|Privacy policy|Modern Slavery Act Transparency Statement|Sitemap|About US| Contact US: help@patsnap.com