Method for hole boring fine processing of ship stern shaft tube
A technology for stern tubes and ships, which is applied in the field of boring and finishing of ship stern tubes. It can solve the problems of insufficient guarantee of grinding quality, low degree of mechanization, and extended processing cycle, so as to shorten the working cycle and improve mechanization. Degree, the effect of reducing labor intensity
- Summary
- Abstract
- Description
- Claims
- Application Information
AI Technical Summary
Problems solved by technology
Method used
Image
Examples
Embodiment Construction
[0056] The method for boring and finishing the ship stern tube of the present invention installs a stern tube finishing device on the stern tube processing and rowing, and uses the wind mill of the stern tube finishing device to process the inner wall of the stern tube processing circle. Grinding.
[0057] As shown in FIG. 1 , the ship stern tube boring and finishing device used in the present invention includes a dynamic and static connector 1 for gas transmission, a wind mill wheel 2 , a wind mill wheel fixing fixture 3 and an air intake duct 4 .
[0058]The dynamic and static connector 1 for gas transmission includes a dynamic chamber joint 11 and a static chamber joint 12, as shown in Figs. 2 and 3 respectively. One end of the movable chamber joint 11 is a flange 111 , and the other end is an inner cavity 112 with an opening, and the inner cavity 112 is provided with a gas delivery interface 113 outside. One end of the static cavity joint 12 also has an open inner cavity ...
PUM
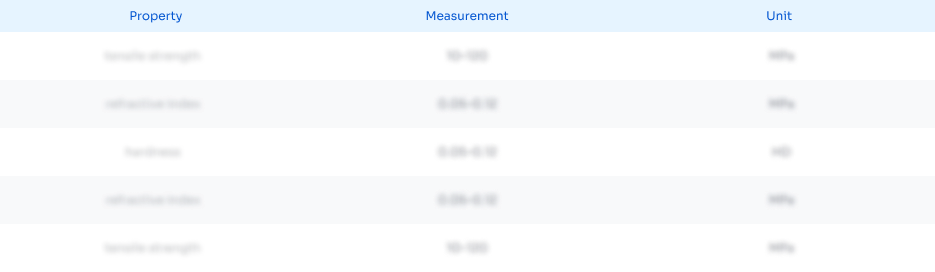
Abstract
Description
Claims
Application Information

- R&D
- Intellectual Property
- Life Sciences
- Materials
- Tech Scout
- Unparalleled Data Quality
- Higher Quality Content
- 60% Fewer Hallucinations
Browse by: Latest US Patents, China's latest patents, Technical Efficacy Thesaurus, Application Domain, Technology Topic, Popular Technical Reports.
© 2025 PatSnap. All rights reserved.Legal|Privacy policy|Modern Slavery Act Transparency Statement|Sitemap|About US| Contact US: help@patsnap.com