Filming method of silicon wafer after IMD CMP
A film-forming method and a technology of silicon wafers, which are applied in the manufacture of electrical components, semiconductor/solid-state devices, circuits, etc., can solve problems such as residual film exceeding the specification, prolonging the production cycle, and large fluctuations in grinding rate, etc., and shorten the production cycle , Etching stability, and the effect of improving product quality
- Summary
- Abstract
- Description
- Claims
- Application Information
AI Technical Summary
Problems solved by technology
Method used
Examples
Embodiment Construction
[0008] The present invention will be further described below in conjunction with embodiment.
[0009] After the silicon wafer IMD CMP, according to the residual film thickness after CMP, the corresponding PCO (growth oxide film) film forming conditions are automatically selected. That is, if the residual film thickness after CMP is thicker, select the PCO condition with less film formation; if the residual film thickness after CMP is thinner, select the corresponding PCO (growth oxide film) condition with more film formation. Therefore, the oxide film formed by PCO is basically at the same level, so that the etching of VIA (contact hole) is relatively stable.
[0010] CMP residual film thickness
PCO film forming conditions
3000-3499 Ȧ
A (growth is 5000 Ȧ)
3500-3999A
B (growth is 4500 Ȧ)
4000-4499 Ȧ
C (growth is 4000 Ȧ)
4500-4999A
D (growth is 3500 Ȧ)
5000-5499A
E (growth is 3000 Ȧ)
[0011] For...
PUM
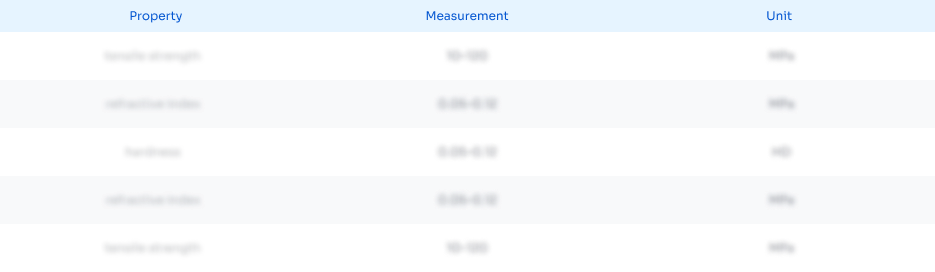
Abstract
Description
Claims
Application Information

- R&D Engineer
- R&D Manager
- IP Professional
- Industry Leading Data Capabilities
- Powerful AI technology
- Patent DNA Extraction
Browse by: Latest US Patents, China's latest patents, Technical Efficacy Thesaurus, Application Domain, Technology Topic, Popular Technical Reports.
© 2024 PatSnap. All rights reserved.Legal|Privacy policy|Modern Slavery Act Transparency Statement|Sitemap|About US| Contact US: help@patsnap.com