Catalytic distillation method of olefine direct epoxidation
A technology of catalytic distillation and epoxidation, applied in chemical industry, organic chemistry, sustainable manufacturing/processing, etc., can solve the problems of complex structure of reaction device, high energy consumption of solvent recovery, and ineffective utilization of reaction heat, etc. Achieve the effects of high utilization rate of reaction heat, reduced energy consumption, and simple device structure
- Summary
- Abstract
- Description
- Claims
- Application Information
AI Technical Summary
Problems solved by technology
Method used
Image
Examples
specific Embodiment approach
[0019] The reaction process that adopts the method for catalytic distillation to carry out olefin epoxidation can have following several specific embodiments, but the present invention is not limited thereto:
[0020] One of the implementation methods:
[0021] For the system of olefins with low boiling point and easy vaporization and the boiling point of the product is lower than the reaction temperature, the olefins can enter the tower from the lower end of the reaction section in one or more stages, and the oxidant hydrogen peroxide and solvent enter the tower from the upper end of the reaction section , After the olefin is vaporized, it mixes with the descending hydrogen peroxide and solvent during the rising process, contacts with the catalyst and reacts. At the same time, the heat released by the reaction vaporizes the solvent, removes the heat, and limits the temperature rise of the reaction section, thereby achieving the purpose of removing heat and controlling the tem...
Embodiment 1
[0033] This example is the direct epoxidation of propylene to propylene oxide.
[0034] The reaction raw materials are 27% industrial hydrogen peroxide, more than 99.9% polymer grade industrial propylene, and the solvent is analytically pure methanol. Hydrogen peroxide is fed into the reaction section of the tower from the upper inlet of the reaction section by a metering pump, and the propylene after decompression and steady flow is metered by a mass flow meter and then enters the tower from the lower inlet of the reaction section. The molar ratio of hydrogen peroxide is 2.5:1. After the device is started, methanol is first injected from the upper part of the reaction section, and after the device runs stably, propylene and hydrogen peroxide are added, and methanol is added at the same time until the molar ratio of propylene to methanol in the reaction section is 1:8. The reaction conditions are as follows: the temperature of the reaction section is controlled at 60°C, the r...
Embodiment 2
[0036] This example is the direct epoxidation of propylene to propylene oxide.
[0037] Reaction raw material and solvent are with embodiment 1. Propylene and hydrogen peroxide are fed in a molar ratio of 4:1, and the molar ratio of propylene to methanol in the reaction section is 1:12. The reaction conditions are: the temperature of the reaction section is controlled at 70°C, the reaction pressure is 0.2MPa (absolute pressure), and the mass space velocity of propylene is 3.5h -1 . Process operation method is the same as embodiment 1. Reaction result: the conversion rate of hydrogen peroxide is 100%, and the selectivity of hydrogen peroxide epoxidation is 97.3%.
PUM
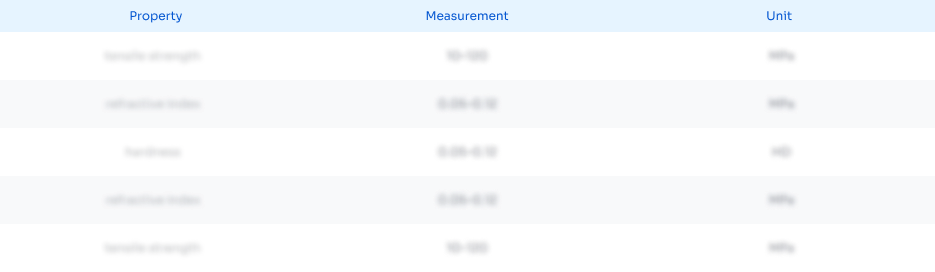
Abstract
Description
Claims
Application Information

- R&D
- Intellectual Property
- Life Sciences
- Materials
- Tech Scout
- Unparalleled Data Quality
- Higher Quality Content
- 60% Fewer Hallucinations
Browse by: Latest US Patents, China's latest patents, Technical Efficacy Thesaurus, Application Domain, Technology Topic, Popular Technical Reports.
© 2025 PatSnap. All rights reserved.Legal|Privacy policy|Modern Slavery Act Transparency Statement|Sitemap|About US| Contact US: help@patsnap.com