Integrated method for modification, activation, treatment delivering and spraying the absorbent
A technology of activation treatment and absorbent, which is applied in the field of flue gas purification, can solve the problems of loss of partial surface activity of absorbent, loss of porosity, low utilization rate of absorbent, etc., to reduce the probability of agglomeration and coagulation increase, appearance The effect of irregular area and rich micro cracks
- Summary
- Abstract
- Description
- Claims
- Application Information
AI Technical Summary
Problems solved by technology
Method used
Image
Examples
Embodiment 1
[0064] Such as figure 1 As shown, one or two or more original absorbents 1 used for the removal of sulfur oxides / nitrogen oxides in flue gas are adjusted to the absorbent to be treated by the metering mechanism 2 according to the required speed (speed adjustable) 3 supply the jet milling device 5, and the jet milling device 5 can select jet mills with different processing capacities on the market according to needs. Under the action of water vapor with a temperature of 250-350°C and an absolute pressure of 0.9-1.3 MPa as the pulverizing airflow 4, the absorbent 3 to be treated is accelerated in the jet pulverization device 5 and collides with each other or with each other at a very high relative speed. The target area is impacted and broken into finer particles, producing abundant micro-cracks, exposing the fresh surface, and mixing and adhering to each other at the same time, so that it becomes the modified and activated absorbent 6. form a gas-solid two-phase flow with the ...
Embodiment 2
[0066] Such as figure 2 As shown, on the basis of Example 1, the injection booster gas 15 is provided at the nozzle 9, so that the absorbent 8 after further modification and activation can obtain a higher injection velocity, so as to meet the needs of a larger space in the flue gas channel 10. Requirements for the cross-section to be mixed with flue gas.
Embodiment 3
[0068] Such as image 3 As shown, on the basis of Embodiment 1, one or more places along the pneumatic conveying pipeline 7 are provided with conveying booster gas 16 to make up for the pulverized airflow 4 after the completion of the crushing treatment of the absorbent 3 to be treated. The remaining pressure cannot meet the insufficient delivery distance or injection speed requirements.
PUM
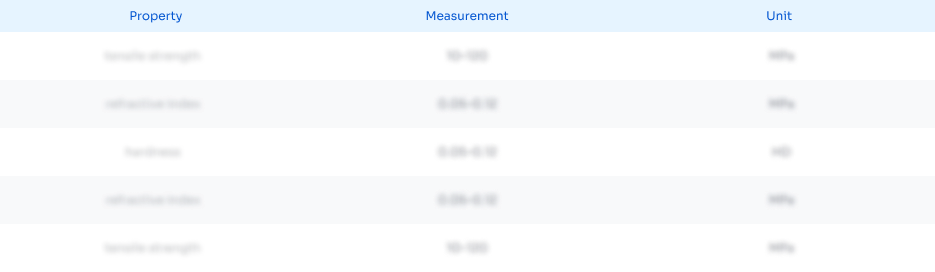
Abstract
Description
Claims
Application Information

- R&D
- Intellectual Property
- Life Sciences
- Materials
- Tech Scout
- Unparalleled Data Quality
- Higher Quality Content
- 60% Fewer Hallucinations
Browse by: Latest US Patents, China's latest patents, Technical Efficacy Thesaurus, Application Domain, Technology Topic, Popular Technical Reports.
© 2025 PatSnap. All rights reserved.Legal|Privacy policy|Modern Slavery Act Transparency Statement|Sitemap|About US| Contact US: help@patsnap.com