Vacuum oxygen blowing decarbon refining furnace smelting stainless steel high carbon region denitrogen method
A vacuum oxygen blowing decarburization and refining furnace technology, applied in the field of stainless steel denitrification in vacuum oxygen blowing decarburization refining furnace, can solve the problems of high cost, complicated process, equipment damage, etc., and achieve light spatter, simple process, and damage small effect
- Summary
- Abstract
- Description
- Claims
- Application Information
AI Technical Summary
Problems solved by technology
Method used
Examples
Embodiment 1
[0022] The requirements for smelting raw materials and smelting furnaces are as follows:
[0023] The double-station platform type vacuum oxygen blowing decarburization refining furnace is adopted. The volume of the furnace is 75t, and the distance from the free space, that is, the slag liquid level to the upper edge of the ladle wall, is 1250mm. Smelted stainless steel: 00Cr12Ti.
[0024] The actual thickness of molten steel slag is 20mm. The molten steel weighs 75.1 tons.
[0025] C%
Si%
Mn%
P%
S%
Cr%
Ni%
Nppm
0.32
0.13
0.18
0.024
0.003
10.82
0.05
230
[0026] The temperature of molten steel before treatment was 1605°C.
[0027] The steps of this embodiment are as follows:
[0028] Time Processing content
[0029] 8:16 The stainless steel molten steel is poured into the ladle of the vacuum oxygen blowing decarburization refining furnace before treatment, and the workin...
Embodiment 2
[0044] The requirements for smelting raw materials and smelting furnaces are as follows:
[0045] The double-station platform type vacuum oxygen blowing decarburization refining furnace is adopted. The volume of the furnace is 75t, and the distance from the free space, that is, the slag liquid level to the upper edge of the ladle wall, is 1250mm.
[0046] The actual thickness of molten steel slag is 28mm.
[0047] The molten steel weighs 73.6 tons.
[0048] Smelted stainless steel: 0Cr18Ni9.
[0049] C%
Si%
Mn%
P%
S%
Cr%
Ni%
Nppm
0.34
0.11
1.21
0.016
0.005
17.36
8.11
376
[0050] The temperature of molten steel before treatment was 1593°C.
[0051] The steps of this embodiment are as follows:
[0052]Time Processing content
[0053] 00:58 The stainless steel molten steel is poured into the ladle of the vacuum oxygen blowing decarburization refining furnace before treatme...
Embodiment 3
[0066] The requirements for smelting raw materials and smelting furnaces are as follows:
[0067] The double-station platform type vacuum oxygen blowing decarburization refining furnace is adopted. The volume of the furnace is 75t, and the distance from the free space, that is, the slag liquid level to the upper edge of the ladle wall, is 1250mm.
[0068] The actual thickness of molten steel slag is 24mm.
[0069] The molten steel weighs 71.8 tons.
[0070] Smelted stainless steel: 0Cr17.
[0071] Chemical composition of molten steel before treatment:
[0072] C%
Si%
Mn%
P%
S%
Cr%
Ni%
Nppm
0.38
0.10
0.24
0.020
0.008
17.01
0.02
359
[0073] The temperature of molten steel before treatment was 1599°C.
[0074] The steps of this embodiment are as follows:
[0075] Time Processing content
[0076] 09:45 Before the treatment, the stainless steel molten steel is poured into t...
PUM
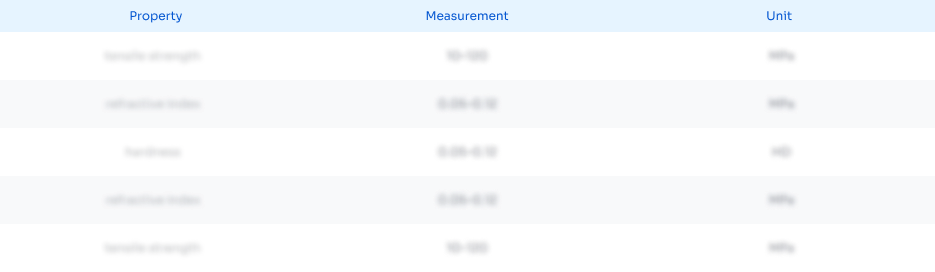
Abstract
Description
Claims
Application Information

- Generate Ideas
- Intellectual Property
- Life Sciences
- Materials
- Tech Scout
- Unparalleled Data Quality
- Higher Quality Content
- 60% Fewer Hallucinations
Browse by: Latest US Patents, China's latest patents, Technical Efficacy Thesaurus, Application Domain, Technology Topic, Popular Technical Reports.
© 2025 PatSnap. All rights reserved.Legal|Privacy policy|Modern Slavery Act Transparency Statement|Sitemap|About US| Contact US: help@patsnap.com