Ultrathin fiberized porcelain plate, its forming process and equipment
A technology for forming equipment and ceramic plates, which is applied to ceramic layered products, other household appliances, chemical instruments and methods, etc., can solve the problems of inability to adapt to the continuous operation requirements of the production line, complex structure of the forming device, and poor corrosion resistance, etc. Achieve the effect of simple molding process steps, low operation and maintenance costs, and long service life
- Summary
- Abstract
- Description
- Claims
- Application Information
AI Technical Summary
Problems solved by technology
Method used
Image
Examples
Embodiment 1
[0046]After the conventional steps of mixing clay raw materials, adding water and stirring, and putting the stirred wet clay into the vacuum mud mixer, press figure 2 The steps shown and image 3 , Figure 4 The plate-shaped forming device shown performs forming and subsequent processes. The cross-section of the outlet of the plate-shaped forming device is shown in Figure 5. The ratio of length to width of the die outlet is 1.8:0.1.
[0047] Wherein, the moisture content of the clay is 15%, and the extrusion pressure is 1000 tons / m 3 , the rolling pressure is 500 tons / m 3 , the drying temperature is 80°C and the time is 2 hours, the bisque firing temperature is 800°C and the time is 2 hours, and the firing temperature is 1300°C and the time is 120 minutes. According to the above method, an ultra-thin fiber porcelain plate with a specification of 3×2×0.003 meters is produced. The green grain layer is circular, elliptical, square or polygonal formed by raised or sunken stra...
Embodiment 2
[0051] The cross-section of the discharge opening is adopted as shown in Figure 6. The length and width dimension ratio of the die discharge opening is 0.8:0.03; the moisture content of the clay is 20%, and the extrusion The pressure is 500 tons / m 3 , the rolling pressure is 300 tons / m 3 , the drying temperature is 250°C and the time is 20 minutes, the bisque firing temperature is 1300°C and the time is 30 minutes, and the firing temperature is 800°C and the time is 30 minutes. All the other are with embodiment 1.
[0052] According to the above-mentioned method, the ultra-thin fiber porcelain plate with a specification of 1.5×1×0.008 meters is produced.
Embodiment 3
[0054] The cross-section of the discharge opening is adopted as shown in Figure 7. The length and width dimension ratio of the die discharge opening is 1: 0.05; the moisture content of the clay is 18%, and the extrusion The pressure is 1000 tons / m 3 , the rolling pressure is 300 tons / m 3 , the drying temperature is 125°C and the time is 1.5 hours, the bisque firing temperature is 900°C and the time is 1 hour, and the firing temperature is 1200°C and the time is 1.2 hours. All the other are with embodiment 1.
[0055] According to the above method, an ultra-thin fiber porcelain plate with a specification of 1 × 1 × 0.008 meters was produced.
PUM
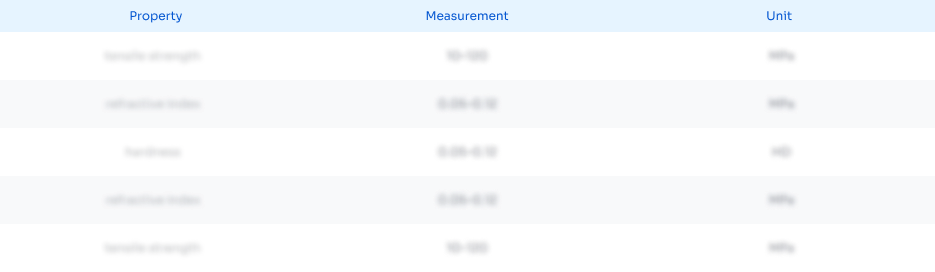
Abstract
Description
Claims
Application Information

- R&D Engineer
- R&D Manager
- IP Professional
- Industry Leading Data Capabilities
- Powerful AI technology
- Patent DNA Extraction
Browse by: Latest US Patents, China's latest patents, Technical Efficacy Thesaurus, Application Domain, Technology Topic, Popular Technical Reports.
© 2024 PatSnap. All rights reserved.Legal|Privacy policy|Modern Slavery Act Transparency Statement|Sitemap|About US| Contact US: help@patsnap.com