Dielectric layer reetching method
A dielectric layer and etch-back technology, which is applied in the manufacture of circuits, electrical components, semiconductors/solid-state devices, etc., can solve the problem of uneven thickness of the dielectric layer and achieve the effect of improving the problem of uneven thickness of the dielectric layer
- Summary
- Abstract
- Description
- Claims
- Application Information
AI Technical Summary
Problems solved by technology
Method used
Image
Examples
Embodiment Construction
[0017] In this embodiment, the ILD layer is planarized according to the method of the present invention to provide a better planarized structure. Such as figure 1 As shown, a semiconductor substrate 10 is provided, with a plurality of elements D distributed in a sparse area 40 with a small number of elements and a dense area 20 with a large number of elements. The elements D are, for example, MOS transistors, capacitor structures (capacitor ) or other logic components (logic devices), while the surface of component D is made of silicon nitride (Si 3 N 4 ), polysilicon (poly-silicon), amorphous silicon (amorphoussilicon), metal or metal nitride and other non-oxygen (Oxygen free) materials. Next, a dielectric layer material is formed to cover the element D in the element sparse region 40 and the element dense region 20, wherein the dielectric layer material is formed of an oxygen-containing (oxygen contained) material, For example, silicon dioxide, doped silicon dioxide (BSG,...
PUM
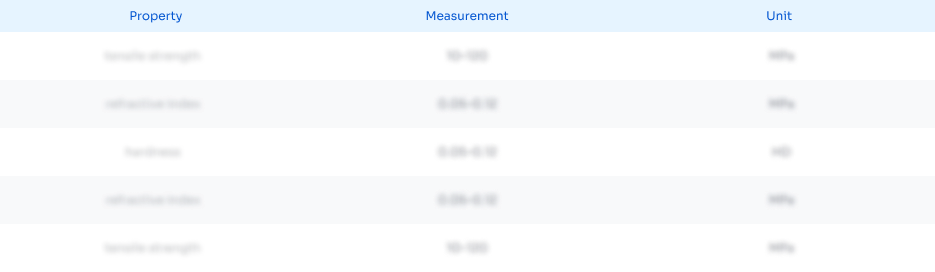
Abstract
Description
Claims
Application Information

- R&D
- Intellectual Property
- Life Sciences
- Materials
- Tech Scout
- Unparalleled Data Quality
- Higher Quality Content
- 60% Fewer Hallucinations
Browse by: Latest US Patents, China's latest patents, Technical Efficacy Thesaurus, Application Domain, Technology Topic, Popular Technical Reports.
© 2025 PatSnap. All rights reserved.Legal|Privacy policy|Modern Slavery Act Transparency Statement|Sitemap|About US| Contact US: help@patsnap.com