Friction materials of polyphenyl ester plastic alloy ultrasonic motor
A plastic alloy and friction material technology, applied in the field of polyphenylene composite materials, can solve problems such as poor bonding performance, low hardness, and insufficient thermal conductivity
- Summary
- Abstract
- Description
- Claims
- Application Information
AI Technical Summary
Problems solved by technology
Method used
Examples
specific Embodiment approach 1
[0004] Embodiment 1: This embodiment is made by mixing polyphenylene and polytetrafluoroethylene, in terms of mass percentage: 5-20% polytetrafluoroethylene, and the balance is polyphenylene.
specific Embodiment approach 2
[0005] Specific Embodiment 2: This embodiment is made by mixing polyphenylene and polytetrafluoroethylene, in terms of mass percentage: 7-15% polytetrafluoroethylene, and the balance is polyphenylene.
specific Embodiment approach 3
[0006] Specific Embodiment Three: This embodiment is made by mixing polyphenylene and polytetrafluoroethylene, in terms of mass percentage: polytetrafluoroethylene is 10%, and the balance is polyphenylene.
PUM
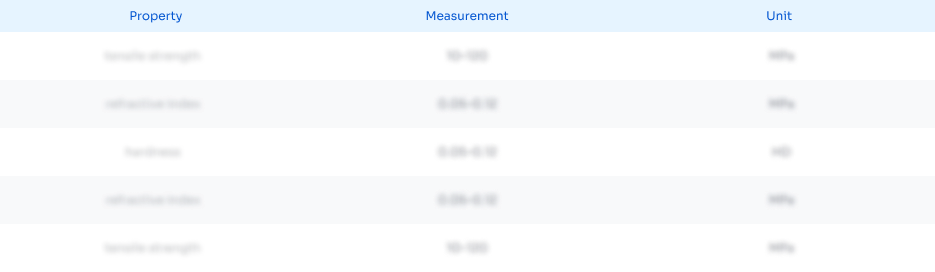
Abstract
Description
Claims
Application Information

- R&D Engineer
- R&D Manager
- IP Professional
- Industry Leading Data Capabilities
- Powerful AI technology
- Patent DNA Extraction
Browse by: Latest US Patents, China's latest patents, Technical Efficacy Thesaurus, Application Domain, Technology Topic, Popular Technical Reports.
© 2024 PatSnap. All rights reserved.Legal|Privacy policy|Modern Slavery Act Transparency Statement|Sitemap|About US| Contact US: help@patsnap.com