Composite welding method and device for silicon carbide reinforced aluminum matrix composite
A technology for silicon carbide and composite welding, applied in welding equipment, metal processing equipment, manufacturing tools, etc., can solve problems affecting welding quality, high frictional resistance, low processing efficiency, etc., and achieve high-efficiency and high-quality composite welding, improve Strength and hardness, effect of reducing welding cost
- Summary
- Abstract
- Description
- Claims
- Application Information
AI Technical Summary
Problems solved by technology
Method used
Image
Examples
Embodiment 2
[0039] like Figure 1-Figure 4 As shown, this embodiment provides a hybrid welding device for silicon carbide reinforced aluminum matrix composite materials, which adopts the hybrid welding method for silicon carbide reinforced aluminum matrix composite materials described in Embodiment 1 for welding, including a hybrid welding system, The hybrid welding system includes a CNC machining table, a laser welding head 1, a friction stir welding head 3 and a controller 9. The CNC machining table is used to fix the workpiece 2 to be welded, and the controller 9 controls the laser welding head according to the thickness of the workpiece 2 to be welded. 1. The power of the laser beam emitted, the laser welding speed v, the stirring depth H and the rotation speed ω of the stirring needle of the friction stir welding processing head 3, and the controller 9 can also control the friction stir welding speed. Among them, the laser welding head 1 and the friction stir welding processing head ...
PUM
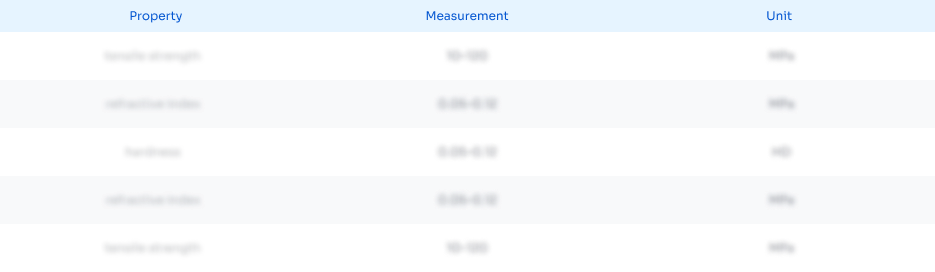
Abstract
Description
Claims
Application Information

- R&D Engineer
- R&D Manager
- IP Professional
- Industry Leading Data Capabilities
- Powerful AI technology
- Patent DNA Extraction
Browse by: Latest US Patents, China's latest patents, Technical Efficacy Thesaurus, Application Domain, Technology Topic, Popular Technical Reports.
© 2024 PatSnap. All rights reserved.Legal|Privacy policy|Modern Slavery Act Transparency Statement|Sitemap|About US| Contact US: help@patsnap.com