Preparation method of spheroidic alpha alumina for grinding and polishing
A technology of α-alumina and spherical shape, which is applied in chemical instruments and methods, polishing compositions containing abrasives, aluminum compounds, etc., can solve the problems that the hardness and surface uniformity of α-alumina cannot meet high-performance polishing, etc. Achieve the effect of excellent cutting force and polishing rate, concentrated distribution and high hardness
- Summary
- Abstract
- Description
- Claims
- Application Information
AI Technical Summary
Problems solved by technology
Method used
Image
Examples
preparation example Construction
[0027] According to a typical embodiment of the present invention, there is provided a preparation method of spherical alpha alumina for grinding and polishing, comprising the following steps:
[0028] S1. The aluminum-containing compound and the grain-oriented growth aid are mixed and reacted in a liquid phase to obtain a prefabricated product.
[0029] S2. The preform is separated, washed and dried to obtain a precursor.
[0030] S3, mixing and calcining the precursor and the composite mineralizer to obtain the spherical α-alumina for grinding and polishing.
[0031] The preparation method of spherical α-alumina for grinding and polishing provided by the present invention, through the liquid phase reaction, the grain directional growth aid is uniformly coated on the surface of the aluminum-containing compound, mixed with the composite mineralizer and calcined, accompanied by the formation of α-alumina. The transformation of the crystal phase, the crystal is transformed from...
Embodiment 1
[0048] The present embodiment provides a preparation method of spherical α-alumina for grinding and polishing, and the steps are as follows:
[0049] S1, 100g of industrial alumina and 0.1g of magnesium chloride are mixed and reacted in liquid phase to obtain a prefabricated product.
[0050] Wherein: the temperature of the liquid phase reaction is 50 DEG C, the reaction time is 10min, and the heating mode is water bath heating.
[0051] S2. The preform is separated, washed and dried to obtain a precursor.
[0052] Wherein: the washing water is distilled water at 50°C, and the mass ratio of the distilled water to the aluminum-containing compound is 2:1.
[0053] S3, mixing and calcining the precursor and the composite mineralizer to obtain the spherical α-alumina for grinding and polishing.
[0054] Among them: the composite mineralizer includes fluoride and boron compound, the fluoride is aluminum fluoride, and the boride is boric acid;
[0055] The mass ratio of the fluor...
Embodiment 2
[0058] The present embodiment provides a preparation method of spherical α-alumina for grinding and polishing, and the steps are as follows:
[0059] S1. 100g of industrial alumina and 0.5g of magnesium chloride are mixed and reacted in a liquid phase to obtain a prefabricated product.
[0060] Wherein: the temperature of the liquid phase reaction is 80°C, the reaction time is 30min, and the heating mode is water bath heating.
[0061] S2. The preform is separated, washed and dried to obtain a precursor.
[0062] Wherein: the washing water is distilled water at 80°C, and the mass ratio of the distilled water to the aluminum-containing compound is 3:1.
[0063] S3, mixing and calcining the precursor and the composite mineralizer to obtain the spherical α-alumina for grinding and polishing.
[0064] Among them: the composite mineralizer includes fluoride and boron compound, the fluoride is calcium fluoride, and the boron is boric acid;
[0065] The mass ratio of the fluoride ...
PUM
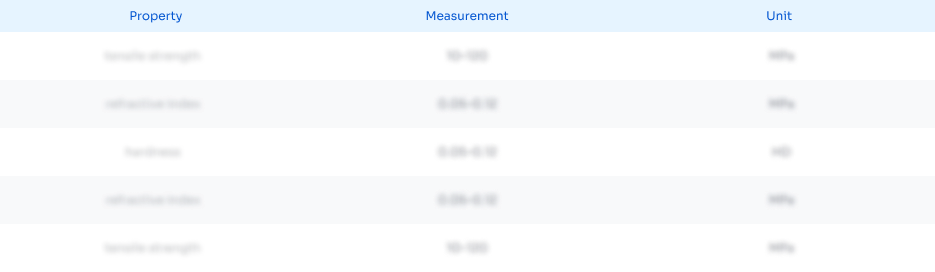
Abstract
Description
Claims
Application Information

- R&D
- Intellectual Property
- Life Sciences
- Materials
- Tech Scout
- Unparalleled Data Quality
- Higher Quality Content
- 60% Fewer Hallucinations
Browse by: Latest US Patents, China's latest patents, Technical Efficacy Thesaurus, Application Domain, Technology Topic, Popular Technical Reports.
© 2025 PatSnap. All rights reserved.Legal|Privacy policy|Modern Slavery Act Transparency Statement|Sitemap|About US| Contact US: help@patsnap.com