Preparation method and application of environment-friendly polyurethane catalyst
A polyurethane catalyst and an environment-friendly technology, applied in the field of preparation of an environment-friendly polyurethane catalyst, can solve the problems of restricting the development of polyurethane and human injury, and achieve the effects of improving yield, simple operation and broad application prospects.
- Summary
- Abstract
- Description
- Claims
- Application Information
AI Technical Summary
Problems solved by technology
Method used
Image
Examples
Embodiment 1
[0036] (1) 0.81g of zinc oxide is dissolved in 200mL of 0.1mol / L dilute hydrochloric acid, and the pH of the solution is adjusted to 3 with dilute hydrochloric acid to obtain an environmentally friendly organic zinc solution;
[0037] (2) 21.6g of tridecanoic acid was dissolved in 100mL of 1mol / L sodium hydroxide solution, heated to 70°C, maintained for 3 hours, and the solid was dissolved to obtain a carboxylate solution;
[0038] (3) adding 100mL environment-friendly organic zinc solution and 100mL valeric acid to the 100ml carboxylate solution obtained in step (2), stirring evenly, heating to 80° C., and reacting for 2 hours to obtain a product solution that generates precipitation; Cooling, vacuum filtration with a Buchner funnel, and repeatedly rinsed with 60°C distilled water for 6 times; the washed product is placed in a 120°C vacuum drying oven for drying to obtain an environmentally friendly organozinc catalyst.
[0039] The catalyst yield obtained in this example was...
Embodiment 2
[0042] (1) 1.36g of zinc chloride is dissolved in 200mL of 0.1mol / L dilute nitric acid, and the pH of the solution is adjusted to be 4 with dilute nitric acid to obtain an environmentally friendly organic zinc solution;
[0043] (2) 14.4g of isooctanoic acid was dissolved in 100mL of 1mol / L sodium hydroxide solution, heated to 60°C, maintained for 3 hours, and the solid was dissolved to obtain a carboxylate solution;
[0044] (3) adding 100mL environment-friendly organic zinc solution and 100mL mineral oil to the 100ml carboxylate solution obtained in step (2), stirring evenly, heating to 70° C., and reacting for 3 hours to obtain a viscous product solution; Cool the solution, use a separating funnel to stand for stratification, separate the water phase, perform vacuum distillation on the organic phase to obtain the product, and repeatedly rinse the product with 50°C distilled water for 8 times; place the washed product in a 100°C vacuum drying oven. Drying is carried out in t...
Embodiment 3
[0048] (1) 1.89g of zinc nitrate was dissolved in 200mL of 0.1mol / L dilute nitric acid, and the pH of the solution was adjusted to 3 with dilute nitric acid to obtain an environmentally friendly organic zinc solution;
[0049] (2) 17.2g of neodecanoic acid was dissolved in 100mL of 1mol / L sodium hydroxide solution, heated to 70°C, maintained for 3 hours, and the solid was dissolved to obtain a carboxylate solution;
[0050](3) in the 100ml carboxylate solution obtained in step (2), add environment-friendly 100mL organic zinc solution and 150mL propionic acid, stir, be heated to 60 ℃, react 4 hours, obtain the product solution that generates precipitation;
[0051] The product solution was cooled, vacuum filtered with a Buchner funnel, and washed with distilled water at 60°C for 7 times; the washed product was placed in a vacuum drying oven at 100°C for drying to obtain an environmentally friendly organozinc catalyst.
[0052] The catalyst yield obtained in this example was 76....
PUM
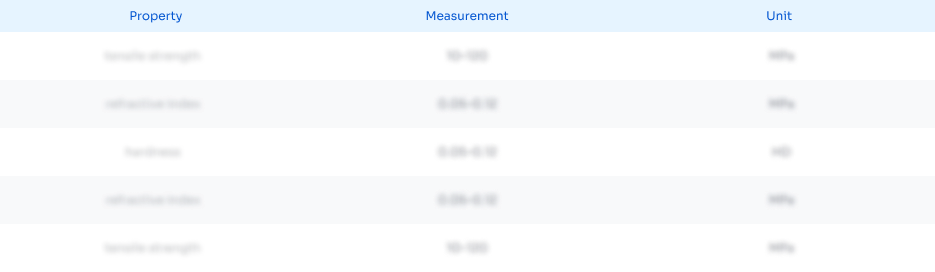
Abstract
Description
Claims
Application Information

- R&D Engineer
- R&D Manager
- IP Professional
- Industry Leading Data Capabilities
- Powerful AI technology
- Patent DNA Extraction
Browse by: Latest US Patents, China's latest patents, Technical Efficacy Thesaurus, Application Domain, Technology Topic, Popular Technical Reports.
© 2024 PatSnap. All rights reserved.Legal|Privacy policy|Modern Slavery Act Transparency Statement|Sitemap|About US| Contact US: help@patsnap.com