Reverse flotation process for synchronously removing silicon and magnesium impurities from collophanite and collecting agent of reverse flotation process
A collophosphate and reverse flotation technology, applied in flotation, solid separation and other directions, can solve the problem that the magnesium-bearing minerals and siliceous gangue minerals cannot be removed at the same time in the collophosphate, and reduce the dosage of flotation reagents, The effect of enhancing the removal effect and improving the sorting efficiency
- Summary
- Abstract
- Description
- Claims
- Application Information
AI Technical Summary
Problems solved by technology
Method used
Image
Examples
Embodiment 1
[0051] For a siliceous calcium phosphate ore in Hubei, the raw ore P 2 O 5 Grade 26.18%, MgO content 2.86%, SiO 2 The content is 18.32%, which is processed according to the following process:
[0052] 1) Crushing the massive collophosphate ore to 1mm, and then grinding, the grinding fineness is -0.074mm, accounting for 87.3%, adding water to adjust the slurry concentration to 25%, and the temperature is about 20 ℃; adding the mass ratio to the slurry is 8:2 sulfur-phosphorus mixed acid was used as pH adjuster, the dosage was 3.2kg / t, and stirred for 0.5min; the mixture of starch and sodium pyrophosphate was added to the pulp as an inhibitor, and the dosage was 0.8kg / t, and stirred for 1min; then added Mixed collector 0.35kg / t for roughing by reverse flotation to obtain product A and foam product A in the tank, the content of MgO in the tank is 1.27%, SiO 2 The content is 13.36%, indicating that the silicon and magnesium impurities can be removed simultaneously. The mixed c...
Embodiment 2
[0058] For a siliceous calcium phosphate mine in Guizhou, the raw ore P 2 O 5 Grade 25.35%, MgO content 2.53%, SiO 2 The content is 21.71%, which is processed according to the following process method:
[0059] 1) Crushing the massive collophosphate ore to 1mm, and then grinding, the grinding fineness is -0.074mm, accounting for 84.8%, adding water to adjust the pulp concentration to 25%, and the temperature is about 20 ℃; adding the mass ratio to the pulp is 8:2 mixed acid of sulfur and phosphorus was used as pH adjuster, the dosage was 2.6kg / t, and stirred for 0.5min; the mixture of starch and sodium pyrophosphate was added to the pulp as an inhibitor, and the dosage was 0.9kg / t, and stirred for 1min; then added The mixed collector 0.31kg / t is subjected to reverse flotation roughing to obtain product A and foam product A in the tank. The mixed collectors used are dodecyl trimethyl ammonium bromide, A mixture of potassium dodecyl phosphate, dodecane and terpene alcohol in ...
Embodiment 3
[0065] For a siliceous calcium phosphate ore in Hubei, the raw ore P 2 O 5 Grade 26.78%, MgO content 2.27%, SiO 2 The content is 19.54%, which is processed according to the following process method:
[0066] 1) Crush the massive collophosphate ore to 1mm, and then grind the ore. The grinding fineness is -0.074mm, accounting for 89.2%. Add water to adjust the slurry concentration to 25%, and the temperature is about 20 °C; 8:2 sulfur-phosphorus mixed acid was used as pH adjuster, the dosage was 3.0kg / t, and stirred for 0.5min; the mixture of starch and sodium pyrophosphate was added to the pulp as an inhibitor, and the dosage was 0.65kg / t, and the stirring was for 1min; then added The mixed collector 0.30kg / t is subjected to reverse flotation and roughing to obtain product A and foam product A in the tank. A mixture of potassium tetradecyl phosphate, diesel oil and terpineol oil in a mass ratio of 35:15:13:23:14;
[0067] 2) Add 1.2kg / t of sulfur-phosphorus mixed acid with ...
PUM
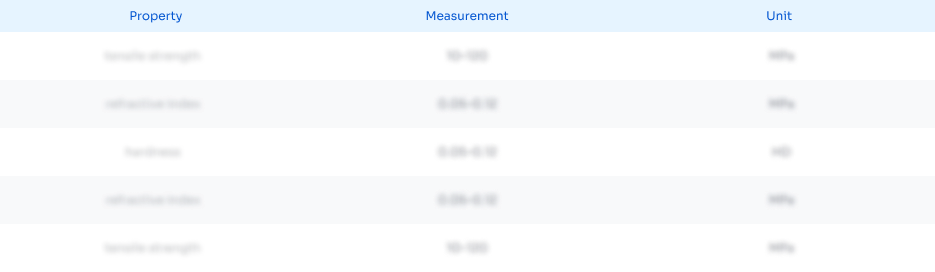
Abstract
Description
Claims
Application Information

- Generate Ideas
- Intellectual Property
- Life Sciences
- Materials
- Tech Scout
- Unparalleled Data Quality
- Higher Quality Content
- 60% Fewer Hallucinations
Browse by: Latest US Patents, China's latest patents, Technical Efficacy Thesaurus, Application Domain, Technology Topic, Popular Technical Reports.
© 2025 PatSnap. All rights reserved.Legal|Privacy policy|Modern Slavery Act Transparency Statement|Sitemap|About US| Contact US: help@patsnap.com