Tempered glass processing technology
A processing technology and tempered glass technology, which is applied in glass tempering, glass manufacturing equipment, manufacturing tools, etc., can solve the high problem of self-explosion of tempered glass, and achieve the effects of reducing glass self-explosion rate, saving water and reducing self-explosion
- Summary
- Abstract
- Description
- Claims
- Application Information
AI Technical Summary
Problems solved by technology
Method used
Image
Examples
Embodiment 1
[0028] A tempered glass processing technology, comprising the following steps:
[0029] Step 1: Cut the glass into glass membranes that meet the specifications, first punch and trim the glass membranes, then grind the edges, and send them into the heating furnace;
[0030] Step 2: Perform the first heating operation on the glass at a heating rate of 6-10°C / 10s to raise the temperature to 180°C, and then perform a second heating operation on the glass at a heating rate of 10°C / min. to 270°C, then the glass was subjected to a third heating operation at a heating rate of 15°C / min, the temperature was raised to 420°C, and finally the glass was subjected to a fourth heating operation at a heating rate of 30°C / min, and the temperature was raised to 650°C °C;
[0031] Step 3: Put the glass on the wind grille for rapid cooling, so that the glass temperature drops to 100°C within 8-10s. When the glass temperature drops to 100°C, stop blowing and take out the glass from the wind grille...
Embodiment 2
[0041] A tempered glass processing technology, comprising the following steps:
[0042] Step 1: Cut the glass into glass membranes that meet the specifications, first punch and trim the glass membranes, then grind the edges, and send them into the heating furnace;
[0043] Step 2: Perform the first heating operation on the glass at a heating rate of 6-10°C / 10s to raise the temperature to 190°C, and then perform a second heating operation on the glass at a heating rate of 10°C / min. to 285°C, then the glass was subjected to a third heating operation at a heating rate of 15°C / min, the temperature was raised to 440°C, and finally the glass was subjected to a fourth heating operation at a heating rate of 30°C / min, and the temperature was raised to 665°C °C;
[0044] Step 3: Put the glass on the wind grille for rapid cooling, so that the glass temperature drops to 100°C within 8-10s. When the glass temperature drops to 100°C, stop blowing and take out the glass from the wind grille; ...
Embodiment 3
[0054] A tempered glass processing technology, comprising the following steps:
[0055] Step 1: Cut the glass into glass membranes that meet the specifications, first punch and trim the glass membranes, then grind the edges, and send them into the heating furnace;
[0056] Step 2: Carry out the first heating operation on the glass at a heating rate of 6-10°C / 10s to raise the temperature to 200°C, and then perform a second heating operation on the glass at a heating rate of 10°C / min, and the temperature rises to 300°C, then the glass was subjected to a third heating operation at a heating rate of 15°C / min, the temperature was raised to 460°C, and finally the glass was subjected to a fourth heating operation at a heating rate of 30°C / min, and the temperature was raised to 680°C °C;
[0057] Step 3: Put the glass on the wind grille for rapid cooling, so that the glass temperature drops to 100°C within 8-10s. When the glass temperature drops to 100°C, stop blowing and take out th...
PUM
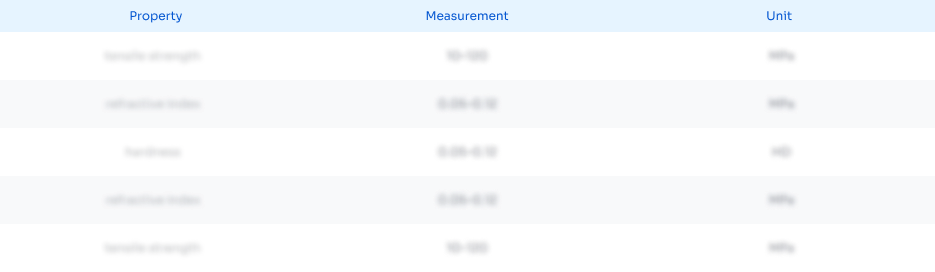
Abstract
Description
Claims
Application Information

- R&D Engineer
- R&D Manager
- IP Professional
- Industry Leading Data Capabilities
- Powerful AI technology
- Patent DNA Extraction
Browse by: Latest US Patents, China's latest patents, Technical Efficacy Thesaurus, Application Domain, Technology Topic, Popular Technical Reports.
© 2024 PatSnap. All rights reserved.Legal|Privacy policy|Modern Slavery Act Transparency Statement|Sitemap|About US| Contact US: help@patsnap.com