Preparation method of battery-grade lithium hydroxide
A lithium hydroxide, battery-level technology, applied in the direction of lithium oxide;/hydroxide, battery recycling, waste collector recycling, etc., can solve the problems of high recycling cost, low purity of lithium products, and increased economic costs, etc., to achieve The effect of reducing lithium recovery cost, improving lithium recovery rate and improving production efficiency
- Summary
- Abstract
- Description
- Claims
- Application Information
AI Technical Summary
Problems solved by technology
Method used
Image
Examples
preparation example Construction
[0028] The invention provides a method for preparing battery-grade lithium hydroxide, comprising:
[0029] Roasting after mixing the waste ternary positive electrode powder and sulfate to obtain a roasted material;
[0030] filtering the calcined material after water immersion to obtain water immersion liquid and water immersion slag;
[0031] After the transformation reaction of the water immersion solution and quicklime, filtration is obtained to obtain transformation lithium liquid and calcium slag;
[0032] After mixing the transformation lithium liquid with the impurity remover and the purifying agent, filter to obtain lithium hydroxide solution and filter residue;
[0033] The lithium hydroxide solution is crystallized to obtain battery grade lithium hydroxide.
[0034] In the present invention, the preparation method of the waste ternary positive electrode powder preferably includes:
[0035] The waste ternary lithium battery is discharged, crushed, pyrolyzed and sor...
Embodiment 1
[0073] Place the waste ternary lithium battery in a 0.8mol / L NaCl solution for discharge treatment. After the discharge is completed, the waste lithium battery is cleaned, dried and crushed. After crushing, it is placed in a rotary kiln for pyrolysis under the protection of nitrogen. The pyrolysis temperature is 300°C, and finally the waste ternary cathode powder is obtained by sorting.
[0074] Mix 500g of the waste ternary positive electrode powder obtained from the pretreatment with 500g of sodium bisulfate evenly, and send it to a high-temperature furnace for calcination at a temperature of 500°C for 1 hour.
[0075] Add the roasted waste ternary positive electrode powder into pure water and stir to leaching, control the liquid-solid ratio of the water immersion to 4:1, the temperature is 80°C, and the time is 1h. The slurry after water immersion is press-filtered to obtain the water immersion liquid For subsequent processes, the water leaching residue is used to recover n...
Embodiment 2
[0081] Place the waste ternary lithium battery in a 1.5mol / L NaCl solution for discharge treatment. After the discharge is completed, the waste lithium battery is cleaned, dried and crushed. After crushing, it is placed in a rotary kiln for pyrolysis under the protection of nitrogen. The pyrolysis temperature is 350°C, and finally the waste ternary cathode powder is obtained by sorting.
[0082] Mix 500g of the pretreated waste ternary cathode powder with 600g of sodium bisulfate evenly, and send it to a high-temperature furnace for calcination at a temperature of 600°C for 2 hours.
[0083] Add the roasted waste ternary positive electrode powder into pure water and stir for leaching, control the liquid-solid ratio of the water immersion to 5:1, the temperature is 60°C, and the time is 2h. The slurry after water immersion is press-filtered to obtain the water immersion liquid For subsequent processes, the water leaching residue is used to recover nickel, cobalt and manganese. ...
PUM
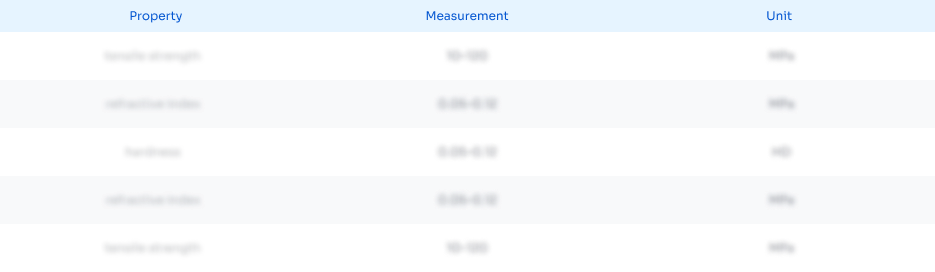
Abstract
Description
Claims
Application Information

- Generate Ideas
- Intellectual Property
- Life Sciences
- Materials
- Tech Scout
- Unparalleled Data Quality
- Higher Quality Content
- 60% Fewer Hallucinations
Browse by: Latest US Patents, China's latest patents, Technical Efficacy Thesaurus, Application Domain, Technology Topic, Popular Technical Reports.
© 2025 PatSnap. All rights reserved.Legal|Privacy policy|Modern Slavery Act Transparency Statement|Sitemap|About US| Contact US: help@patsnap.com