Electric furnace for waste mercury and catalyst mercury recovery
A waste mercury catalyst and electric furnace technology, applied in the direction of improving process efficiency, etc., can solve the problems of small equipment capacity, low production efficiency, agglomeration, etc., and achieve the effects of uniform heating, improved service life and furnace temperature uniformity
- Summary
- Abstract
- Description
- Claims
- Application Information
AI Technical Summary
Problems solved by technology
Method used
Image
Examples
Embodiment 1
[0018] Refer to the attached figure 1 - 3. The electric furnace mainly includes a furnace cover 11, a furnace body 1, a furnace tank 2, a heating element, and a heating control system. The furnace tank 2 is located inside the furnace body 1, the outer heating element 5 is located outside the furnace tank 2, and the inner heating element 7 Arranged in the heating chamber 8 in the furnace tank 2, the heating control system adjusts the heating power of the inner heating element 7 and the outer heating element 5 according to the temperature in the furnace tank 2, the temperature of the electric furnace is controlled at 750 °C, and the temperature control accuracy is ±1 °C .
[0019] In the embodiment of the present invention, the furnace body 1 is composed of an outer shell, a furnace lining, and an external heating element support body. The outer shell is made of square steel and thin common steel plate, and the load-bearing shell adopts a steel frame, which has sufficient streng...
Embodiment 2
[0027] The heating control system adjusts the heating power of the inner heating element 7 and the outer heating element 5 according to the temperature inside the furnace tank 2. The temperature of the electric furnace is controlled at 550°C, and the temperature control accuracy is ±1°C; the heating chamber 8 is evenly distributed into 2 widths and set to 200mm The small chamber 4, the lower part of the small chamber 4 in the furnace tank 2 is the same cone, and the small chamber 4 and the upper part of the furnace tank 2 are provided with a space of 200mm; the inner heating element 7 is divided into 7 groups of heating bodies that can be independently disassembled 7 layers, the inner heating element 7 is in the form of resistance wire wrapped on the corundum porcelain tube; there is one main feeding port and two auxiliary feeding ports on the furnace cover.
Embodiment 3
[0029] The heating control system adjusts the heating power of the inner heating element 7 and the outer heating element 5 according to the temperature inside the furnace tank 2. The temperature of the electric furnace is controlled at 800°C, and the temperature control accuracy is ±1°C; the heating chamber 8 is evenly distributed into 4 or more widths Set the small chamber 4 of 400mm, the lower part of the small chamber 4 in the furnace tank 2 is the same cone, and the small chamber 4 and the upper part of the furnace tank 2 are provided with a space of 400mm; the inner heating element 7 is divided into 4 or more groups and can be dismantled independently The installed heating body is divided into 4 or more layers up and down, and the inner heating element 7 is in the form of a resistance wire wound on a silicon carbide rod or a silicon molybdenum rod; the furnace cover 11 is provided with 1 main feeding port and 6 auxiliary feeding ports .
[0030] According to the electric ...
PUM
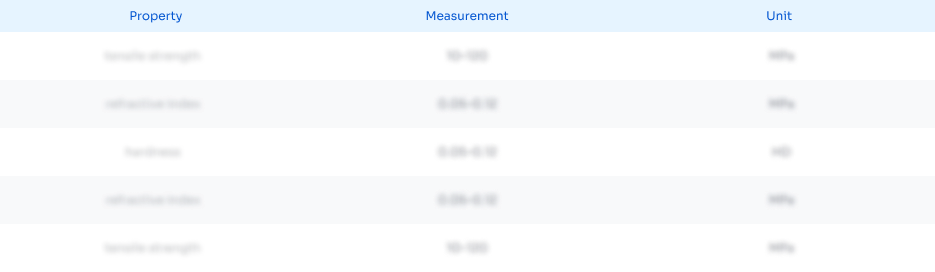
Abstract
Description
Claims
Application Information

- Generate Ideas
- Intellectual Property
- Life Sciences
- Materials
- Tech Scout
- Unparalleled Data Quality
- Higher Quality Content
- 60% Fewer Hallucinations
Browse by: Latest US Patents, China's latest patents, Technical Efficacy Thesaurus, Application Domain, Technology Topic, Popular Technical Reports.
© 2025 PatSnap. All rights reserved.Legal|Privacy policy|Modern Slavery Act Transparency Statement|Sitemap|About US| Contact US: help@patsnap.com