Alumina fiber reinforced mullite ceramic-based composite material and preparation method thereof
An alumina fiber and composite material technology, which is applied in the field of fiber-reinforced ceramic composite materials, can solve the problems of no interface layer protection, low alumina powder sintering activity, and decreased mechanical properties of composite materials, and achieves a simple, easy, and excellent preparation method. High temperature mechanical properties and the effect of improving impregnation efficiency
- Summary
- Abstract
- Description
- Claims
- Application Information
AI Technical Summary
Problems solved by technology
Method used
Image
Examples
Embodiment 1
[0026] S1. Preparation of mullite slurry: add mullite powder, mullite sol and citric acid into a ball mill tank, add large and small balls, set the speed of the ball mill to 150rpm, and mill for 8 hours to obtain ceramic with a yield of 20wt%. Mullite slurry. The mass ratio of mullite powder, mullite sol and citric acid is 40:150:1, and the ceramic yield of mullite sol is 20wt%.
[0027] S2. Pretreatment of alumina fiber preform: Arrange alumina fiber satin in a muffle furnace, heat to 500°C for 3 hours, and cool down to room temperature naturally to obtain alumina fiber preform after removal of sizing agent.
[0028] S3, preparation of lanthanum phosphate interface layer: adopt existing preparation methods such as CN110983757A to prepare lanthanum phosphate precursor solution, after stirring and mixing lanthanum nitrate solution (0.4mol / L) and phosphoric acid solution (0.4mol / L) at 1°C, Obtain the lanthanum phosphate precursor solution; impregnate the alumina fiber preform f...
Embodiment 2
[0032] S1. Preparation of mullite slurry: add mullite powder, mullite sol and citric acid into a ball mill tank, add large and small balls, set the speed of the ball mill to 300rpm, and mill for 8 hours to obtain ceramic with a yield of 40wt%. Mullite slurry. The mass ratio of mullite powder, mullite sol and citric acid is 80:200:2, and the ceramic yield of mullite sol is 10wt%.
[0033] S2. Pretreatment of the alumina fiber preform: Arrange the alumina fiber twill in a muffle furnace, heat to 600°C for 1 hour, and cool down to room temperature naturally to obtain the alumina fiber preform after removing the sizing agent.
[0034] S3. Preparation of lanthanum phosphate interface layer: after stirring and mixing lanthanum nitrate solution (0.6mol / L) and phosphoric acid solution (0.6mol / L) at 2°C, a lanthanum phosphate precursor solution is obtained; The fiber prefabricated body was impregnated with the lanthanum phosphate precursor solution and reacted at 50°C for 2h, then it ...
Embodiment 3
[0038]S1. Preparation of mullite slurry: add mullite powder, mullite sol and citric acid into a ball mill tank, add large and small balls, set the speed of the ball mill to 500rpm, and mill for 8 hours to obtain ceramic with a yield of 60wt%. Mullite slurry. The mass ratio of mullite powder, mullite sol and citric acid is 100:100:3, and the ceramic yield of mullite sol is 15wt%.
[0039] S2. Pretreatment of alumina fiber preform: Arrange alumina fiber plain weave in a muffle furnace, heat to 550°C for 1.5h, and cool down to room temperature naturally to obtain alumina fiber preform after removal of sizing agent.
[0040] S3. Preparation of lanthanum phosphate interface layer: after stirring and mixing lanthanum nitrate solution (0.5mol / L) and phosphoric acid solution (0.5mol / L) at 1°C, a lanthanum phosphate precursor solution is obtained; The fiber prefabricated body was impregnated with the lanthanum phosphate precursor solution and reacted at 60°C for 1.5h, then it was take...
PUM
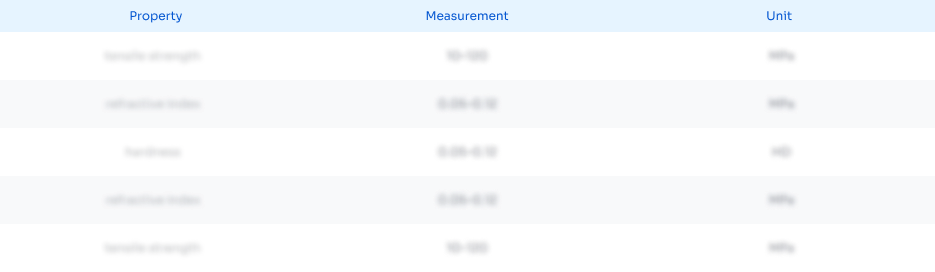
Abstract
Description
Claims
Application Information

- R&D
- Intellectual Property
- Life Sciences
- Materials
- Tech Scout
- Unparalleled Data Quality
- Higher Quality Content
- 60% Fewer Hallucinations
Browse by: Latest US Patents, China's latest patents, Technical Efficacy Thesaurus, Application Domain, Technology Topic, Popular Technical Reports.
© 2025 PatSnap. All rights reserved.Legal|Privacy policy|Modern Slavery Act Transparency Statement|Sitemap|About US| Contact US: help@patsnap.com