Thick-wall pipeline weld joint multi-stage heating device and heating method
A heating device and pipeline technology, applied in induction heating devices, auxiliary devices, induction heating, etc., can solve the problems of increasing manufacturing costs, increasing power supply power, and unavoidable skin effect, so as to avoid cold welding and overheating , skin effect reduction, avoid the effect of skin effect
- Summary
- Abstract
- Description
- Claims
- Application Information
AI Technical Summary
Problems solved by technology
Method used
Image
Examples
Embodiment Construction
[0047] The structure and features of the present invention will be described in detail below in conjunction with the drawings and embodiments. It should be noted that various modifications can be made to the embodiments disclosed herein, therefore, the embodiments disclosed in the specification should not be regarded as limitations on the present invention, but only as examples of embodiments, and its purpose is to make the present invention The features of the invention are self-evident.
[0048] Such as figure 1 , figure 2 As shown, the thick-walled pipe weld multi-stage heating device of the present invention includes an electrode group 1 , a liftable gantry 2 , a left squeeze roller 3 , a welding platform 4 and a right squeeze roller 5 . The liftable gantry 2 is fixed on the welding platform 4, and the electrode group 1 is suspended below the middle of the liftable gantry 2, and the height of the electrode group 1 can be adjusted by adjusting the height of the liftable...
PUM
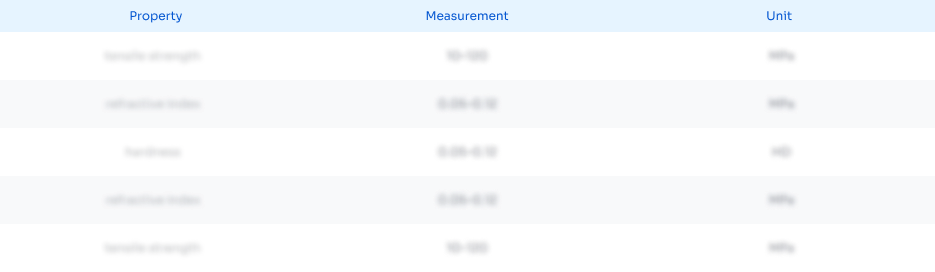
Abstract
Description
Claims
Application Information

- R&D Engineer
- R&D Manager
- IP Professional
- Industry Leading Data Capabilities
- Powerful AI technology
- Patent DNA Extraction
Browse by: Latest US Patents, China's latest patents, Technical Efficacy Thesaurus, Application Domain, Technology Topic, Popular Technical Reports.
© 2024 PatSnap. All rights reserved.Legal|Privacy policy|Modern Slavery Act Transparency Statement|Sitemap|About US| Contact US: help@patsnap.com