Method for separating rare earth and aluminum from ionic rare earth mine leachate
An ionic rare earth and leaching solution technology, which is applied in the field of separation of rare earth and aluminum, can solve the problems of high residual aluminum and large loss of rare earth, and achieve the effects of simple operation, improved recovery rate, and improved utilization rate
- Summary
- Abstract
- Description
- Claims
- Application Information
AI Technical Summary
Problems solved by technology
Method used
Examples
Embodiment 1
[0024] The mass concentrations of rare earth and aluminum in ionic rare earth mine leachate are 1.94g / L and 0.68g / L respectively. Take 50L mine leachate and add ammonium bicarbonate to adjust the pH of the solution to 7.5. Precipitation is formed. After standing for a certain period of time, filter and wash The filter residue S1 can be obtained. Filter residue S1 is mixed with NaOH, the amount of NaOH added (as Na 2 O) and Al in slag 2 o 3 The molar ratio of the mixture is 1.5:1, and after mixing evenly, place it in a muffle furnace at 400°C for 1.5 hours to obtain roasted slag S2. The roasted slag S2 was leached in an aqueous solution, the liquid-solid ratio of the leaching process was 5, the temperature was 60°C, the stirring time was 2 hours, and the stirring speed was 200 r / min. After the reaction, filter and wash to obtain the filter residue S3 and the filtrate L1. During the process, the recovery rate of rare earth was 95.8%, and the removal rate of aluminum was 96.8...
Embodiment 2
[0026] The mass concentrations of rare earth and aluminum in ionic rare earth mine leachate are 1.52g / L and 0.36g / L respectively. Take 50L mine leachate and add ammonium bicarbonate to adjust the pH of the solution to 9.0. Precipitation is formed. After standing for a certain period of time, filter and wash The filter residue S1 can be obtained. Filter residue S1 with NaOH and Na 2 CO 3 Mixed, NaOH and Na 2 CO 3 The molar ratio is 5, the amount of alkali added (as Na 2 O) and Al in slag 2 o 3 The molar ratio of the mixture is 1.8:1, and after mixing evenly, place it in a muffle furnace at 500°C for calcination for 40 minutes to obtain calcination slag S2. The roasted slag S2 was leached in an aqueous solution with a liquid-solid ratio of 4, a temperature of 80°C, a stirring time of 1.5 h, and a stirring rate of 300 r / min. After the reaction, filter and wash to obtain the filter residue S3 and the filtrate L1. During the process, the recovery rate of rare earth was 97.2...
Embodiment 3
[0028] The mass concentrations of rare earth and aluminum in ionic rare earth mine leachate are 1.12g / L and 0.49g / L respectively. Take 50L of mine leachate and add ammonium bicarbonate to adjust the pH of the solution to 10.5. Precipitation is formed. After standing for a certain period of time, filter and wash The filter residue S1 can be obtained. Filter residue S1 is mixed with NaOH, the amount of NaOH added (as Na 2 O) and Al in slag 2 o 3 The molar ratio of the mixture is 2.1:1, and after mixing evenly, place it in a muffle furnace at 600°C for 30 minutes for calcination to obtain calcination slag S2. The roasted slag S2 was leached in an aqueous solution, the liquid-solid ratio of the leaching process was 3, the temperature was 90°C, the stirring time was 1 h, and the stirring speed was 250 r / min. After the reaction, filter and wash to obtain the filter residue S3 and the filtrate L1. During the process, the recovery rate of rare earth was 98.5%, and the removal rate...
PUM
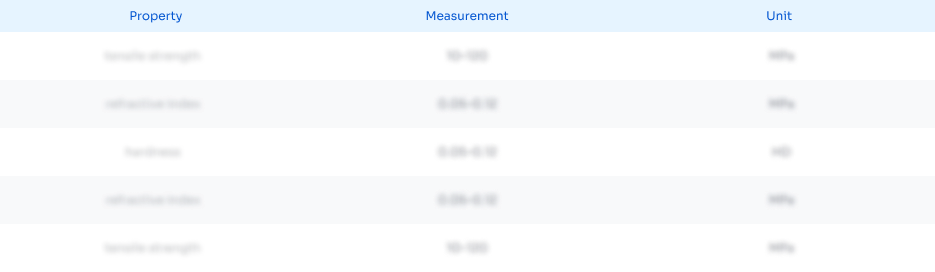
Abstract
Description
Claims
Application Information

- Generate Ideas
- Intellectual Property
- Life Sciences
- Materials
- Tech Scout
- Unparalleled Data Quality
- Higher Quality Content
- 60% Fewer Hallucinations
Browse by: Latest US Patents, China's latest patents, Technical Efficacy Thesaurus, Application Domain, Technology Topic, Popular Technical Reports.
© 2025 PatSnap. All rights reserved.Legal|Privacy policy|Modern Slavery Act Transparency Statement|Sitemap|About US| Contact US: help@patsnap.com