Continuous casting and rolling preparation method of novel zinc alloy wire
A continuous casting and rolling, zinc alloy technology, applied in metal rolling, metal material coating process, coating and other directions, can solve the problems of poor toughness, fracture, and immature preparation technology of zinc-based copper-titanium alloy, and achieve the solution The effect of industrialization
- Summary
- Abstract
- Description
- Claims
- Application Information
AI Technical Summary
Problems solved by technology
Method used
Image
Examples
Embodiment 1
[0023] A continuous casting and rolling preparation method for a novel zinc alloy wire, comprising the following steps:
[0024] (1) Design Zn-Cu-Ti-Ce alloy, wherein the mass percentage of each element is: Cu: 0.7-0.9%; Ti: 0.08-0.1%; Ce: 0.3-0.35%; individual content of other impurities ≤ 0.01% , total ≤ 0.05%; Zn balance.
[0025] (2) Use a vacuum resistance furnace to smelt Zn-3.6Ce master alloy, use pure zinc and pure cerium as raw materials, after the pure zinc is melted at 650°C, add pure cerium into the zinc melt through the feeding port, and keep it warm for 0.5h, It is then poured into rod-shaped ingots.
[0026] (3) Zn-Cu-Ti-Ce alloy is prepared in an induction furnace with a capacity of 2t, and the purchased pure zinc ingot, Zn-10Cu and Zn-3Ti master alloy and self-made Zn-3.6Ce master alloy are added to the induction furnace together. In the furnace, the melting temperature is controlled at 640°C-660°C. When the melt temperature exceeds 640°C, it is kept for 20 ...
Embodiment 2
[0030] A continuous casting and rolling preparation method for a novel zinc alloy wire, comprising the following steps:
[0031] (1) Design Zn-Cu-Ti-Ce alloy, wherein the mass percentage of each element is: Cu: 0.7-0.9%; Ti: 0.08-0.1%; Ce: 0.3-0.35%; individual content of other impurities ≤ 0.01% , total ≤ 0.05%; Zn balance.
[0032] (2) Use a vacuum resistance furnace to smelt Zn-3.6Ce master alloy, use pure zinc and pure cerium as raw materials, after the pure zinc is melted at 650°C, add pure cerium into the zinc melt through the feeding port, and keep it warm for 0.5h, It is then poured into rod-shaped ingots.
[0033] (3) Zn-Cu-Ti-Ce alloy is prepared in an induction furnace with a capacity of 2t, and the purchased pure zinc ingot, Zn-10Cu and Zn-3Ti master alloy and self-made Zn-3.6Ce master alloy are added to the induction furnace together. In the furnace, the melting temperature is controlled at 640°C-660°C. When the melt temperature exceeds 640°C, it is kept for 20 ...
PUM
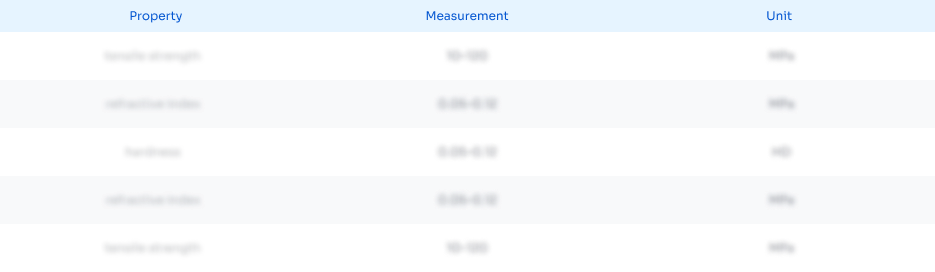
Abstract
Description
Claims
Application Information

- Generate Ideas
- Intellectual Property
- Life Sciences
- Materials
- Tech Scout
- Unparalleled Data Quality
- Higher Quality Content
- 60% Fewer Hallucinations
Browse by: Latest US Patents, China's latest patents, Technical Efficacy Thesaurus, Application Domain, Technology Topic, Popular Technical Reports.
© 2025 PatSnap. All rights reserved.Legal|Privacy policy|Modern Slavery Act Transparency Statement|Sitemap|About US| Contact US: help@patsnap.com