Method for removing carbon deposition on inner wall of air inlet pipe in CVD (Chemical Vapor Deposition) grown graphene powder
A graphene powder and air intake pipe technology, applied in the graphene field, can solve problems such as increased energy consumption, reduced pyrolysis efficiency, and air flow blockage, and achieves the effects of saving production costs, improving service life, and shortening intervals
- Summary
- Abstract
- Description
- Claims
- Application Information
AI Technical Summary
Problems solved by technology
Method used
Image
Examples
Embodiment 1
[0033] Embodiment 1: a method for removing carbon deposits on the inner wall of the intake pipe in a CVD-grown graphene powder, comprising the following steps:
[0034] S1. Insert the graphite inlet pipe into the liquid copper through the lifting device, and then pass the mixed gas of methane / nitrogen into the liquid copper through the graphite inlet pipe, grow graphene powder in the liquid copper, and the graphene powder grows continuously for 8- After 12 hours, disconnect the methane, keep the nitrogen flow constant, and suspend the growth of graphene powder;
[0035]S2. By adjusting the heating power, the temperature of the liquid copper is kept at 1100°C to 1600°C, and the preferred temperature of the liquid copper is 1150°C to 1400°C; in this embodiment, the temperature of the lower part of the graphite intake pipe is raised to Within the temperature range where carbon deposits and oxygen can react, ensure that the carbon deposits on the inner wall of the graphite inlet p...
Embodiment 2
[0046] Embodiment 2: the specific implementation steps of this embodiment are as follows:
[0047] 1) Insert the graphite inlet pipe into the liquid copper at 1290°C through the lifting device, and then pass the methane / nitrogen mixed gas into the liquid copper through the graphite inlet pipe. The flow rates of methane and nitrogen are 4SLM / 30SLM respectively, and grow in the liquid copper Graphene powder, grow continuously for 8 hours, cut off methane, and suspend the growth of graphene powder;
[0048] 2) Adjust the heating power so that the temperature of the liquid copper is at 1300°C;
[0049] 3) Move the gas outlet at the lower part of the graphite inlet pipe out of the liquid copper surface by a lifting device at a distance of 2cm; after 1.5min, feed the oxygen / nitrogen mixed gas, wherein the flow rates of oxygen and nitrogen are 2SLM / 20SLM respectively;
[0050] 4) After the oxygen / nitrogen mixed gas is introduced for 2 minutes, the oxygen is disconnected, the nitroge...
Embodiment 3
[0053] Embodiment 3: the specific implementation steps of this embodiment are as follows:
[0054] 1) Insert the graphite inlet pipe into the liquid copper at 1220°C through the lifting device, and then pass the methane / nitrogen mixed gas into the liquid copper through the graphite inlet pipe. The flow rates of methane and nitrogen are 4.5SLM / 30SLM respectively, in the liquid copper Grow graphene powder, grow continuously for 10 hours, cut off methane, and suspend the growth of graphene powder;
[0055] 2) Adjust the heating power so that the temperature of the liquid copper is at 1250°C;
[0056] 3) Move the gas outlet at the lower part of the graphite inlet pipe out of the liquid copper surface by a lifting device at a distance of 4cm; after 50s, feed oxygen / nitrogen mixed gas, wherein the flow rates of oxygen and nitrogen are 3SLM / 20SLM respectively;
[0057] 4) After the oxygen / nitrogen mixed gas is introduced for 1 minute, the oxygen is disconnected, the nitrogen flow ra...
PUM
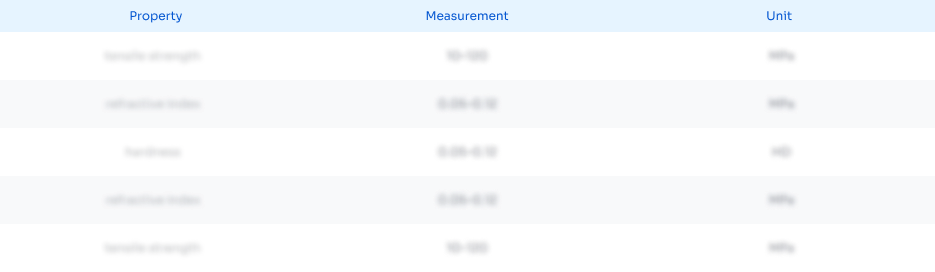
Abstract
Description
Claims
Application Information

- Generate Ideas
- Intellectual Property
- Life Sciences
- Materials
- Tech Scout
- Unparalleled Data Quality
- Higher Quality Content
- 60% Fewer Hallucinations
Browse by: Latest US Patents, China's latest patents, Technical Efficacy Thesaurus, Application Domain, Technology Topic, Popular Technical Reports.
© 2025 PatSnap. All rights reserved.Legal|Privacy policy|Modern Slavery Act Transparency Statement|Sitemap|About US| Contact US: help@patsnap.com