Processing equipment and processing method of anti-dazzle glass
A processing equipment and anti-glare technology, applied in the field of anti-glare glass processing equipment, can solve the problems of flash point generation, poor uniformity of anti-glare surface particles, etc., and achieve the effect of reducing cleaning
- Summary
- Abstract
- Description
- Claims
- Application Information
AI Technical Summary
Problems solved by technology
Method used
Image
Examples
no. 1 example
[0093] In the first embodiment, when two groups of process groups process the same surface to be processed of the same glass substrate to be processed, as Figure 6 As shown, in the first group 45 and the second group 46, the ion emission directions of the first plasma generating device 411 and the second plasma generating device 421 are oppositely arranged, that is, the first plasma generating device 411, the second plasma generating device 421 in the first group 45 The ion emission direction of the second plasma generation device 421 is toward the second group 46, and the ion emission directions of the first plasma generation device 411 and the second plasma generation device 421 in the second group 46 are toward the first group 45; The chamber 47 is equipped with a rotating table, which drives the carrier 10 to rotate, such as 180°, so as to enter the second group 46, and make the glass substrates to be processed face the same surface in the first group 45 and the second gro...
no. 2 example
[0094] In the second embodiment, when two groups of process groups 40 process different surfaces to be processed of the same glass substrate to be processed, as Figure 7 As shown, in the first group 45 and the second group 46, the ion emission directions of the first plasma generating device 411 and the second plasma generating device 421 are oppositely arranged; in this embodiment, the conversion chamber 47 is provided with a translation platform, and the translation platform The direction of translation is parallel to the side-by-side direction of the first group 45 and the second group 46, and perpendicular to the moving direction of the carrier 10, so as to drive the carrier 10 to move so as to enter the second group 46, and make the glass substrate to be processed on the carrier 10 In the first group 45 and the second group 46 , different surfaces face the plasma generating devices therein, that is, the surfaces to be processed facing the first plasma generating device 41...
PUM
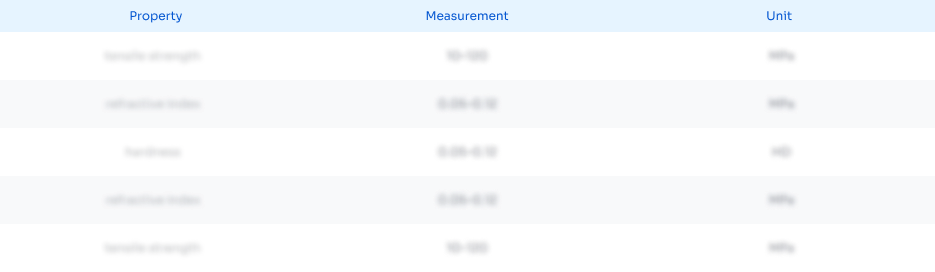
Abstract
Description
Claims
Application Information

- R&D Engineer
- R&D Manager
- IP Professional
- Industry Leading Data Capabilities
- Powerful AI technology
- Patent DNA Extraction
Browse by: Latest US Patents, China's latest patents, Technical Efficacy Thesaurus, Application Domain, Technology Topic, Popular Technical Reports.
© 2024 PatSnap. All rights reserved.Legal|Privacy policy|Modern Slavery Act Transparency Statement|Sitemap|About US| Contact US: help@patsnap.com