Preparation method of hexamethylenediamine
A technology of hexamethylenediamine and adiponitrile, which is applied in the field of preparation of hexamethylenediamine, can solve problems such as reduction, low efficiency, and activity decline, and achieve the effects of good stability, reduced post-processing energy consumption, and reduced catalyst cost
- Summary
- Abstract
- Description
- Claims
- Application Information
AI Technical Summary
Problems solved by technology
Method used
Examples
Embodiment 1
[0040] First add 6g Raney cobalt catalyst (A=298.7ml / min g cat ), 200g ethanol solvent, 3.5g 15% LiOH·H 2O water solution, 8.8 g deionized water. Then replace with nitrogen and hydrogen respectively three times, and pressurize the hydrogen to 3MPa. Turn on the stirring, the stirring rate is 800rpm, and the temperature is raised. When the reaction temperature rises to 90° C., open the hydrogen valve and keep the hydrogen outlet pressure reducing valve at 5 MPa. Open the adiponitrile feed pump at 0.4g / g cat Adiponitrile was poured into the reaction kettle at a flow rate of min. During the reaction, the temperature was maintained at 90° C. and the pressure was 5 MPa. A total of 200 g of adiponitrile was fed. After the feed is complete, when the instantaneous hydrogen absorption rate drops to 0, the reaction is stopped, the temperature is lowered, filtered, and a sample is taken for analysis.
[0041] It took a total of 90 minutes from the start of feeding to the stop of the ...
Embodiment 2
[0043] First add 12g Raney cobalt catalyst (A=348.9ml / min·g cat ), 200g ethanol solvent, 9.8g 15% LiOH·H 2 O water solution, 11.0 g deionized water. Then replace with nitrogen and hydrogen respectively three times, and pressurize the hydrogen to 3MPa. Turn on the stirring, the stirring rate is 800rpm, and the temperature is raised. When the reaction temperature rises to 95° C., open the hydrogen valve and keep the hydrogen outlet pressure reducing valve at 4 MPa. Open the adiponitrile feed pump, at 0.8g / g cat Adiponitrile was poured into the reaction kettle at a flow rate of 1 min. During the reaction, the temperature was maintained at 95° C., the pressure was 4 MPa, and a total of 300 g of adiponitrile was fed. After the feed is complete, when the instantaneous hydrogen absorption rate drops to 0, the reaction is stopped, the temperature is lowered, filtered, and a sample is taken for analysis.
[0044] It took a total of 40 minutes from the start of feeding to the stop ...
Embodiment 3
[0046] First add 5g Raney cobalt catalyst (A=251.3ml / min·g cat ), 200g ethanol solvent, 1.2g 15% LiOH·H 2 O water solution, 4.9 g deionized water. Then replace with nitrogen and hydrogen respectively three times, and pressurize the hydrogen to 3MPa. Turn on the stirring, the stirring rate is 800rpm, and the temperature is raised. When the reaction temperature rises to 100° C., open the hydrogen valve and keep the hydrogen outlet pressure reducing valve at 6 MPa. Open the adiponitrile feed pump at 0.2g / g cat Adiponitrile was pumped into the reaction kettle at a flow rate of min. During the reaction, the temperature was maintained at 100° C., the pressure was 6 MPa, and a total of 100 g of adiponitrile was fed. After the feed is complete, when the instantaneous hydrogen absorption rate drops to 0, the reaction is stopped, the temperature is lowered, filtered, and a sample is taken for analysis.
[0047] It took a total of 108 minutes from the start of feeding to the stop of...
PUM
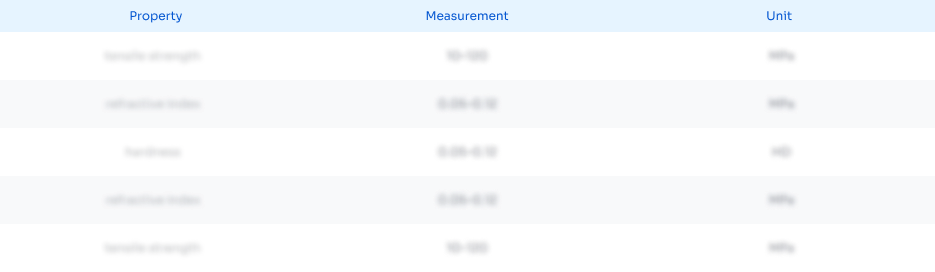
Abstract
Description
Claims
Application Information

- Generate Ideas
- Intellectual Property
- Life Sciences
- Materials
- Tech Scout
- Unparalleled Data Quality
- Higher Quality Content
- 60% Fewer Hallucinations
Browse by: Latest US Patents, China's latest patents, Technical Efficacy Thesaurus, Application Domain, Technology Topic, Popular Technical Reports.
© 2025 PatSnap. All rights reserved.Legal|Privacy policy|Modern Slavery Act Transparency Statement|Sitemap|About US| Contact US: help@patsnap.com