Server, printed circuit board and press-fit manufacturing method of printed circuit board
A technology of printed circuit boards and production methods, which is applied in the fields of printed circuit manufacturing, laminated printed circuit boards, printed circuits, etc., can solve the problems of poor stability of circuit board products, affect product delivery, and high product scrap rate, and achieve improvement of voids problems, and the effect of improving resin voids
- Summary
- Abstract
- Description
- Claims
- Application Information
AI Technical Summary
Problems solved by technology
Method used
Image
Examples
Embodiment 1
[0060] The present invention improves the problems of delamination and resin voids in lamination through high-speed plate pressing control technology, false copper design technology in empty areas, and PP glue content resin flow control technology.
[0061] In a preferred embodiment of the present invention, false copper (copper point or copper block) is added to the open area; the thick copper area increases the PP glue content (RC-72 to RC-75 or RC-77), and it will improve The void problem caused by the loss of pressure in the thick copper area.
[0062] In the present invention, adjust as follows for pressing production mode:
[0063] ①Number of laminated board layers: 2pnl / layer, 2 layers / stack; ②Arrangement method: 10 sheets of kraft paper above and below the chassis,
[0064] Add 5 sheets of kraft paper between each layer, and add aluminum sheets above and below the copper foil; ③The heating rate is ≥4°C / min.
[0065] In a preferred embodiment of the present invention,...
Embodiment 2
[0074] PP glue content resin flow control technology includes:
[0075] The thick copper area will increase the glue content of PP, from RC-72 to RC-75, the glue content will gradually increase, and the fluidity will increase in turn.
[0076] High-speed sheet press control technology includes:
[0077] Step 1: Dehumidify PP for 3 hours before production;
[0078] Step 2: Bake the browned board at a temperature of 100°C for 50 minutes and a heating rate of ≥4°C / min;
[0079] Step 3, typesetting: 2pnl / layer, 2 layers / stack, 10 sheets above and below the chassis, 5 sheets between layers, and aluminum sheets outside the copper foil;
[0080] Step 4, press plate.
Embodiment 3
[0082] In one embodiment of the present invention, the PP glue content resin flow control technology includes:
[0083] The thick copper area increases the glue content of PP, from RC-72 to RC-77. The gel content gradually increases, and the fluidity increases in turn.
[0084] High-speed sheet press control technology includes:
[0085] Step 1: Dehumidify PP for 5 hours before production;
[0086] Step 2: Bake the browned plate at a temperature of 130°C for 70 minutes; the heating rate is ≥4°C / min;
[0087] Step 3, typesetting: 2pnl / layer, 2 layers / stack, 10 sheets above and below the chassis, 5 sheets between layers, and aluminum sheets outside the copper foil;
[0088] Step 4, press plate.
PUM
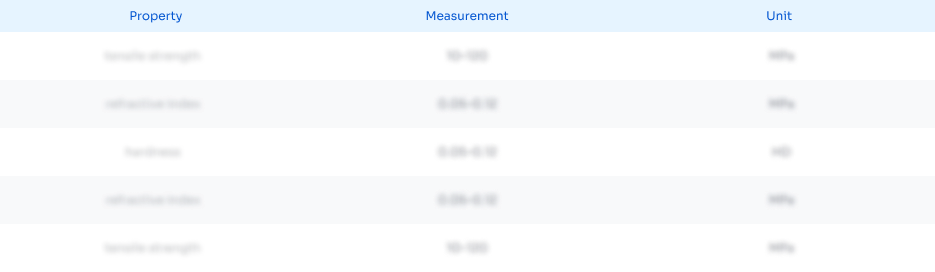
Abstract
Description
Claims
Application Information

- R&D
- Intellectual Property
- Life Sciences
- Materials
- Tech Scout
- Unparalleled Data Quality
- Higher Quality Content
- 60% Fewer Hallucinations
Browse by: Latest US Patents, China's latest patents, Technical Efficacy Thesaurus, Application Domain, Technology Topic, Popular Technical Reports.
© 2025 PatSnap. All rights reserved.Legal|Privacy policy|Modern Slavery Act Transparency Statement|Sitemap|About US| Contact US: help@patsnap.com