Single-screw feeding optimization method and system based on discrete element method
An optimization method and single-screw technology, applied in design optimization/simulation, special data processing applications, geometric CAD, etc., can solve problems such as unsatisfactory engineering requirements, insufficient output, continuous material blockage, etc., to achieve improved spatial layout, Improve the precision of optimized design and ensure the effect of screw extrusion effect
- Summary
- Abstract
- Description
- Claims
- Application Information
AI Technical Summary
Problems solved by technology
Method used
Image
Examples
Embodiment Construction
[0031] The present invention is described in further detail below in conjunction with accompanying drawing:
[0032] Such as figure 1 As shown, a single-screw feed optimization method based on the discrete element method includes the following steps:
[0033] Step 1), construct the three-dimensional model of the discrete units of each part of the screw extruder, and establish the overall assembly model of the screw extruder;
[0034] The three-dimensional model of each part of the discrete unit of the screw extruder is constructed by three-dimensional software, and the three-dimensional model of each part of the discrete unit includes a feed hopper 1, a barrel 3, an elbow 2 and a screw 4 connecting the funnel and the barrel, and The 3D model is imported into the pre-processing software ANSA, the model is as figure 2 shown;
[0035] Step 2), use the pre-processing software to clean up the overall assembly model of the screw extruder and divide the mesh to obtain the finite ...
PUM
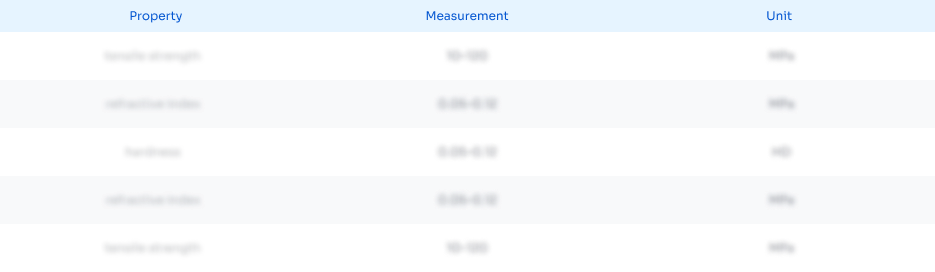
Abstract
Description
Claims
Application Information

- Generate Ideas
- Intellectual Property
- Life Sciences
- Materials
- Tech Scout
- Unparalleled Data Quality
- Higher Quality Content
- 60% Fewer Hallucinations
Browse by: Latest US Patents, China's latest patents, Technical Efficacy Thesaurus, Application Domain, Technology Topic, Popular Technical Reports.
© 2025 PatSnap. All rights reserved.Legal|Privacy policy|Modern Slavery Act Transparency Statement|Sitemap|About US| Contact US: help@patsnap.com