Composite molten steel refining additive
A compound refining and additive technology, which is applied in the field of compound refining additives for molten steel, can solve the problems of difficult to fully remove deoxidized inclusions, slow slag in LF refining furnace, and inability to dissolve lime quickly, so as to shorten the reduction refining time and achieve significant comprehensive economic benefits. , the effect of shortening the refining time
Inactive Publication Date: 2004-03-17
重庆工业高等专科学校
View PDF0 Cites 1 Cited by
- Summary
- Abstract
- Description
- Claims
- Application Information
AI Technical Summary
Problems solved by technology
[0003] 1. The use of a relatively single Al deoxidizer failed to truly realize the multi-component composite deoxidation of molten steel
[0004] 2. Deoxidized inclusions are difficult to fully remove
[0005] 3. The lime (or synthetic slag) added during the tapping process cannot be quickly dissolved into slag (the melting point of lime is as high as 2130°C)
[0006] 4. The LF refining furnace is slow to melt slag, and the refining effects such as desulfurization, deoxidation, and adsorption inclusions are not ideal
[0007] 5. The whole foam slag submerged arc refining cannot be realized on LF
[0008] 6. It takes longer time for LF refining and heating, which affects the smooth progress of UHP(LD)-LF-CC process, affects the increase of continuous casting ratio, and affects steel output
Method used
the structure of the environmentally friendly knitted fabric provided by the present invention; figure 2 Flow chart of the yarn wrapping machine for environmentally friendly knitted fabrics and storage devices; image 3 Is the parameter map of the yarn covering machine
View moreImage
Smart Image Click on the blue labels to locate them in the text.
Smart ImageViewing Examples
Examples
Experimental program
Comparison scheme
Effect test
Embodiment Construction
[0036] Embodiment of the present invention sees table 1:
[0037] Table 1:
[0038]
[0039] The content of aluminum in the aluminum ashes should be 15% (or more than 15%) of the weight of the aluminum ashes in the above-mentioned each embodiment.
[0040] Optimum chemical composition distribution ratio is shown in Table 2 in the composite refining additive of the present invention:
[0041] name
the structure of the environmentally friendly knitted fabric provided by the present invention; figure 2 Flow chart of the yarn wrapping machine for environmentally friendly knitted fabrics and storage devices; image 3 Is the parameter map of the yarn covering machine
Login to View More PUM
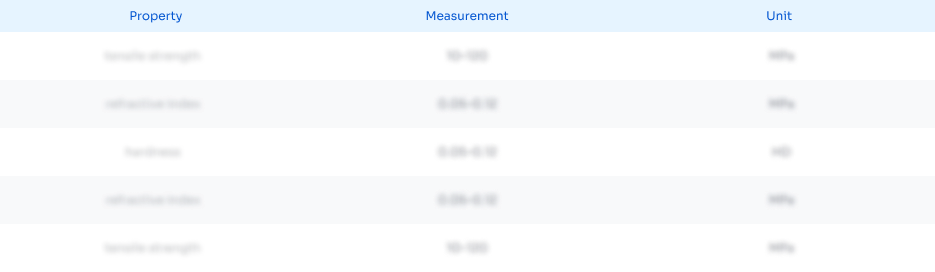
Abstract
This invention provides a molten steel composite refining additive. The said additive by wt.% includes aluminium ash 10-50% (aluminium content at least being 15% of ash wt.), metallurgical furnace slag 10-60%, carbide 5-65%, limestone 1-10% and witherite 1-10%. This additive is used for the oxidable slag tapping process of steel smelting furnace such as electric furnace, converter, etc. and for refining furnace to make the oxidable molten steel proceed polybasic composite oxygen removal, sulphur removal and quick deoxidated impurity inclusion removal, and at the same time, it enhances quick dissolution of added slagging material and quick slag forming.
Description
Technical field: [0001] The invention relates to a composite refining additive for molten steel used in the iron and steel industry. Background technique: [0002] The main process of modern steelmaking is converter-refining furnace-continuous casting-(LD-LF-CC) and ultra-high power electric furnace-refining furnace-continuous casting (UHP-LF-CC). The application of enhanced smelting technologies such as super oxygen supply, molten iron hot charging, scrap preheating, and oxygen burner fluxing has further shortened the oxidation and refining time of molten steel, and the popularization and application of high-efficiency continuous casting has made the billet forming speed of molten steel faster than that of traditional processes. substantial improvement. So shortening the time of LF refining outside the furnace becomes the key to increasing the output of the steelmaking process, increasing the continuous casting ratio, and ensuring the smooth flow of the "three ones" proces...
Claims
the structure of the environmentally friendly knitted fabric provided by the present invention; figure 2 Flow chart of the yarn wrapping machine for environmentally friendly knitted fabrics and storage devices; image 3 Is the parameter map of the yarn covering machine
Login to View More Application Information
Patent Timeline

Patent Type & Authority Patents(China)
IPC IPC(8): C21C7/04
Inventor 任正德雷亚杨治明庞福如
Owner 重庆工业高等专科学校
Features
- R&D
- Intellectual Property
- Life Sciences
- Materials
- Tech Scout
Why Patsnap Eureka
- Unparalleled Data Quality
- Higher Quality Content
- 60% Fewer Hallucinations
Social media
Patsnap Eureka Blog
Learn More Browse by: Latest US Patents, China's latest patents, Technical Efficacy Thesaurus, Application Domain, Technology Topic, Popular Technical Reports.
© 2025 PatSnap. All rights reserved.Legal|Privacy policy|Modern Slavery Act Transparency Statement|Sitemap|About US| Contact US: help@patsnap.com